- In Dedication
- Submitting Your Content
Defining Steels
- Steel Grades
- Coatings for PHS
- Coating Friction
- Microstructural Components
- Forming and Formability of AHSS
- Elastic Modulus
- Yield Strength
- Tensile Strength
- Total Elongation
- Uniform Elongation
- Tensile Testing
- Improvement by Metallurgical Approaches
- Edge Stretching Tests
- Bend Testing
- Bulge and Dome Testing
- Friction and Friction Testing
High Strain Rate Testing
- Delayed Cracking (Hydrogen Embrittlement)
- Circle Grid Strain Analysis (CGSA)
- Non-Linear Strain Paths (Stress-Based FLCs)
- Engineering Stress-Strain vs. True Stress-Strain
- Global vs Local Formability
- True Fracture Strain
- Shear Fracture
- Correcting Springback
- Laser Blanking
- Shear Affected Zone
- Lubrication
- Coil Processing:Straightening & Leveling
- PHS Production Methods
- PHS Simulation
- PHS Tailored Products
- PHS Automotive Applications and Usage
- Tube Forming
- Hydroforming
- Roll Forming
- Simulation Inputs
- Crash Management
- Press Tonnage Predictions
- Quality Control
- Industry 4.0 and AHSS Applications
- Additive Mfg for Sheet Metal Forming Tools
- Introduction
- AHSS and Electrode Geometry
- Coating Effects
- Other RSW Considerations
- Spot Weld Strength Improvement by PWHT
- Post-Heat Conduction CTS Improvement
- RSW of 22MnB5 at Overlaps
- Manufacturing Issues
- RSW of 3T Stack Up
- RSW of 4T Stack Up
- Higher than Expected Strengths
- Weld Testing and Fracture Modes
- Spot Welds Fatigue Strength
- Analyze Hydrogen Induced Cracking Susceptibility
- Liquid Metal Embrittlement Study
- RSW Failure Prediction
- LME Simulation During RSW
- Modelling RSW of AHSS
- HS Boron Methodologies
- Weld Quality with Modular Weld Head
- Fatigue of GMAW-P Lap Joints
- Role of Coatings in Defect Formation AHSS welds
- HAZ Properties of GMAW DP 600
GMAW of Dissimilar AHSS Sheets
- Laser Welding Processes and Applications
- Effect GA-Coating Evolution PHS
- Effect GA-Coating Weight PHS
- LME in Zn-coated 3rd Gen steels
- Adding Colloidal Graphite to Al-Si-Coated PHS
- Hybrid Laser-Arc Welding (HLAW) Pore Formation and Prevention
Hot cracking investigation in HSS laser welding with multi-scale modelling approach
- Improvement of Delayed Cracking in Laser Weld of AHSS and 980 3rd Gen AHSS
- FSSW Method for Joining Ultra-Thin Steel Sheet
- HF Welding Parameters and Procedures
- Magnetic Pulse Welding
- Hybrid Welding Procedures
- Mechanical Joining
- Key Issues: RSW Steel and Aluminium Joints
- Capacitive Discharge Welding
- Aluminium/Steel Using Interlayer
- Aluminium/Steel Using Cover Plates
- REM of Aluminium/Steel
- Ultrasonic Assisted RSW
- Process, Microstructure and Fracture Mode of Thick Stack-Ups of Aluminum Alloy to AHSS Dissimilar Spot Joints
- Solid State Welding of Steel to Aluminum
- Joint Strength in Laser Welding of DP to Aluminium
- Automotive Welding Process Comparisons
- AHSS Insights Blog

Transformation Induced Plasticity (TRIP)
- Transformation Induced Plasticity Effect
The microstructure of Transformation Induced Plasticity (TRIP) steels contains a matrix of ferrite, with retained austenite, martensite, and bainite present in varying amounts. Production of TRIP steels typically requires the use of an isothermal hold at an intermediate temperature, which produces some bainite. Higher silicon and carbon content of TRIP steels result in significant volume fractions of retained austenite in the final microstructure. Figure 1 shows a schematic of TRIP steel microstructure, with Figure 2 showing a micrograph of an actual sample of TRIP steel. Figure 3 compares the engineering stress-strain curve for HSLA steel to a TRIP steel curve of similar yield strength.
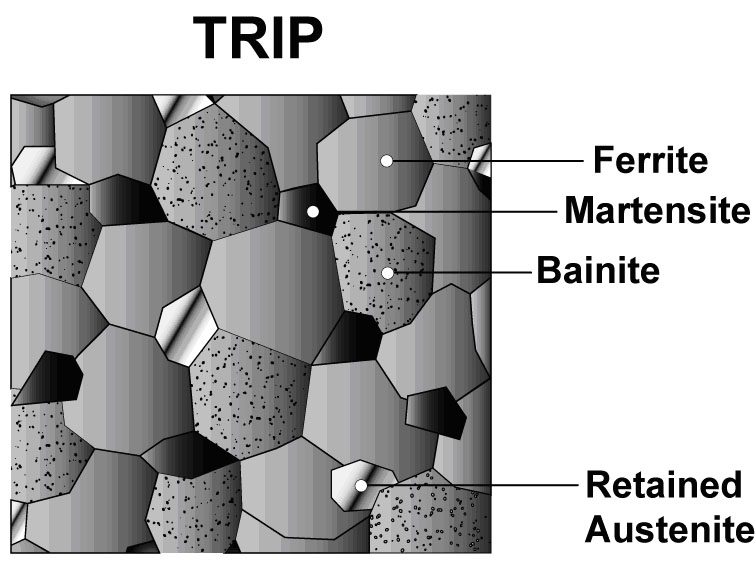
Figure 1: Schematic of a TRIP steel microstructure showing a matrix of ferrite, with martensite, bainite and retained austenite as the additional phases.
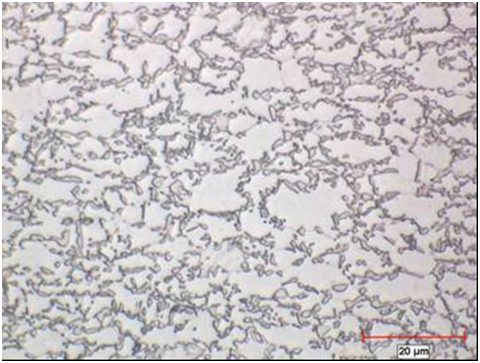
Figure 2: Micrograph of Transformation Induced Plasticity steel.
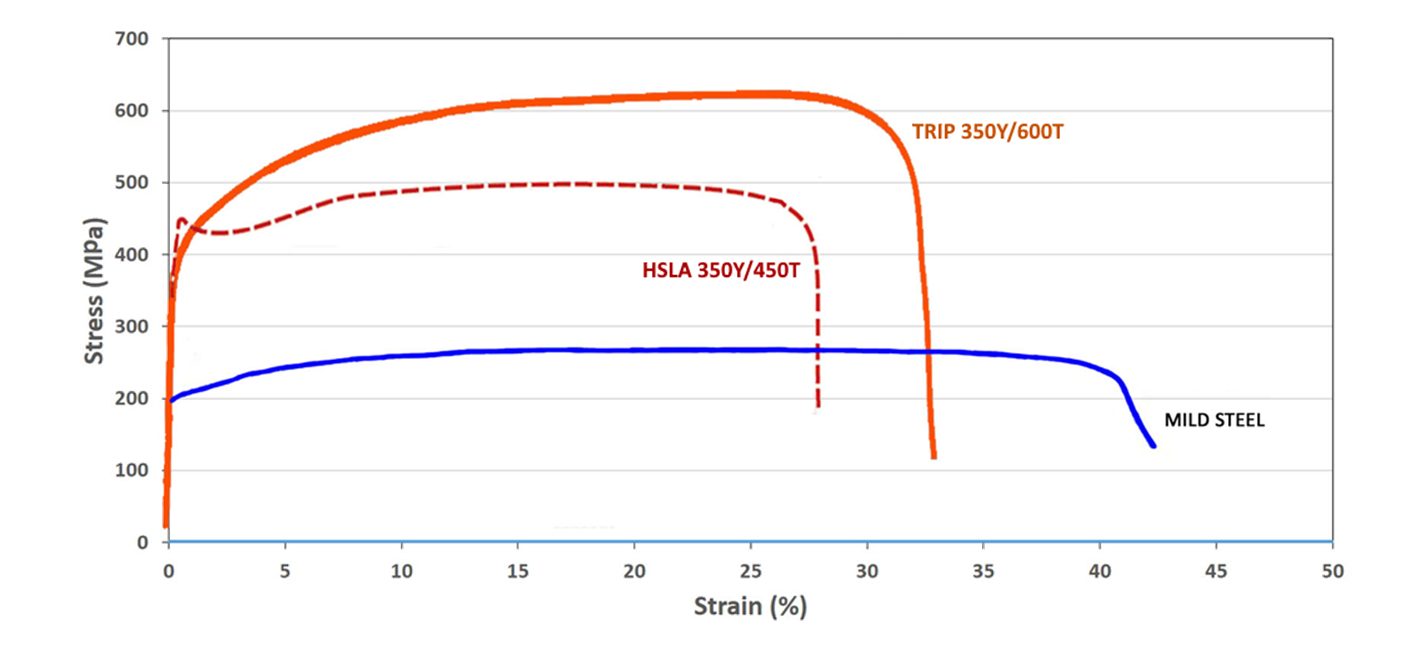
Figure 3: A comparison of stress strain curves for mild steel, HSLA 350/450, and TRIP 350/600. K-1
During deformation, the dispersion of hard second phases in soft ferrite creates a high work hardening rate, as observed in the DP steels. However, in TRIP steels the retained austenite also progressively transforms to martensite with increasing strain, thereby increasing the work hardening rate at higher strain levels. This is known as the TRIP Effect . This is illustrated in Figure 4, which compares the engineering stress-strain behavior of HSLA, DP and TRIP steels of nominally the same yield strength. The TRIP steel has a lower initial work hardening rate than the DP steel, but the hardening rate persists at higher strains where work hardening of the DP begins to diminish. Additional engineering and true stress-strain curves for TRIP steel grades are shown in Figure 5.
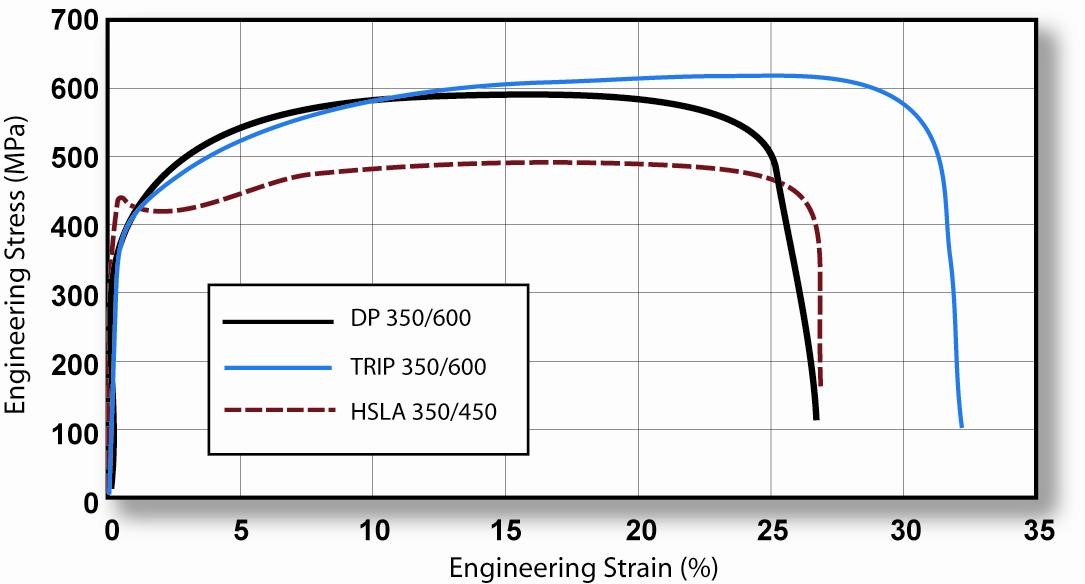
Figure 4: TRIP 350/600 with a greater total elongation than DP 350/600 and HSLA 350/450. K-1
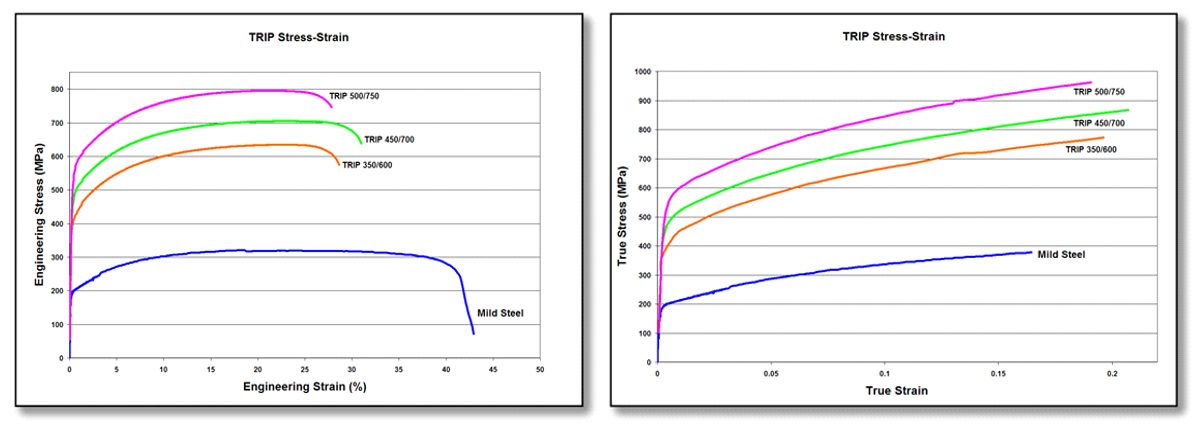
Figure 5: Engineering stress-strain (left graphic) and true stress-strain (right graphic) curves for a series of TRIP steel grades. Sheet thickness: TRIP 350/600 = 1.2mm, TRIP 450/700 = 1.5mm, TRIP 500/750 = 2.0mm, and Mild Steel = approx. 1.9mm. V-1
The strain hardening response of TRIP steels are substantially higher than for conventional HSS, resulting in significantly improved formability in stretch deformation. This response is indicated by a comparison of the n-value for the grades. The improvement in stretch formability is particularly useful when designers take advantage of the improved strain hardening response to design a part utilizing the as-formed mechanical properties. High n-value persists to higher strains in TRIP steels, providing a slight advantage over DP in the most severe stretch forming applications.
Austenite is a higher temperature phase and is not stable at room temperature under equilibrium conditions. Along with a specific thermal cycle, carbon content greater than that used in DP steels are needed in TRIP steels to promote room-temperature stabilization of austenite. Retained austenite is the term given to the austenitic phase that is stable at room temperature.
Higher contents of silicon and/or aluminum accelerate the ferrite/bainite formation. These elements assist in maintaining the necessary carbon content within the retained austenite. Suppressing the carbide precipitation during bainitic transformation appears to be crucial for TRIP steels. Silicon and aluminum are used to avoid carbide precipitation in the bainite region.
The carbon level of the TRIP alloy alters the strain level at which the TRIP Effect occurs. The strain level at which retained austenite begins to transform to martensite is controlled by adjusting the carbon content. At lower carbon levels, retained austenite begins to transform almost immediately upon deformation, increasing the work hardening rate and formability during the stamping process. At higher carbon contents, retained austenite is more stable and begins to transform only at strain levels beyond those produced during forming. At these carbon levels, retained austenite transforms to martensite during subsequent deformation, such as a crash event.
TRIP steels therefore can be engineered to provide excellent formability for manufacturing complex AHSS parts or to exhibit high strain hardening during crash deformation resulting in excellent crash energy absorption.
The additional alloying requirements of TRIP steels degrade their resistance spot-welding behavior. This can be addressed through weld cycle modification, such as the use of pulsating welding or dilution welding. Table 1 provides a list of current production grades of TRIP steels and example automotive applications:
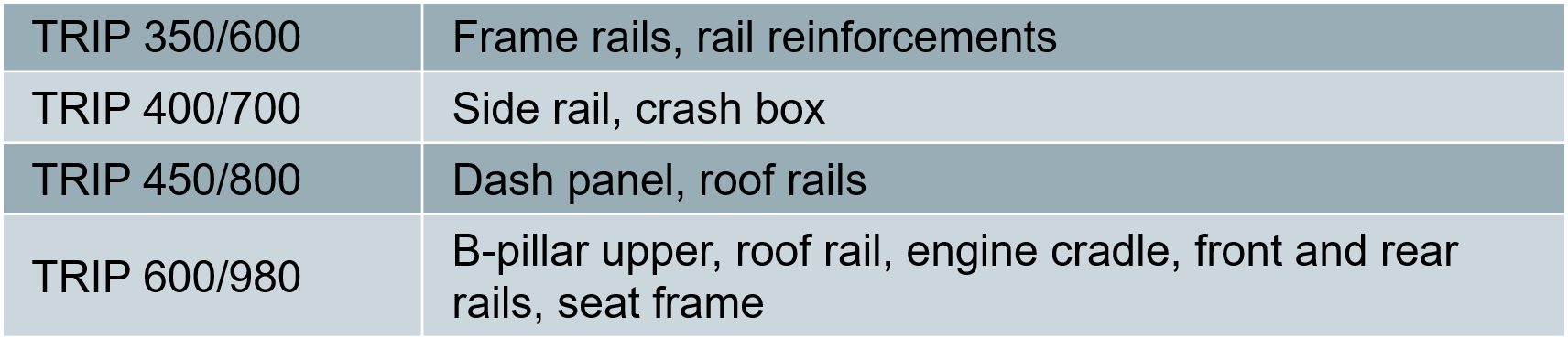
Table 1: Current Production Grades Of TRIP Steels And Example Automotive Applications.
Some of the specifications describing uncoated cold rolled 1st Generation transformation induced plasticity (TRIP) steel are included below, with the grades typically listed in order of increasing minimum tensile strength and ductility. Different specifications may exist which describe hot or cold rolled, uncoated or coated, or steels of different strengths. Many automakers have proprietary specifications which encompass their requirements. • ASTM A1088, with the terms Transformation induced plasticity (TRIP) steel Grades 690T/410Y and 780T/440Y A-22 • JFS A2001, with the terms JSC590T and JSC780T J-23 • EN 10338, with the terms HCT690T and HCT780T D-18 • VDA 239-100, with the terms CR400Y690T-TR and CR450Y780T-TR V-3 • SAE J2745, with terms Transformation Induced Plasticity (TRIP) 590T/380Y, 690T/400Y, and 780T/420Y S-18
Austenite is not stable at room temperature under equilibrium conditions. An austenitic microstructure is retained at room temperature with the combined use of a specific chemistry and controlled thermal cycle. Deformation from sheet forming provides the necessary energy to allow the crystallographic structure to change from austenite to martensite. There is insufficient time and temperature for substantial diffusion of carbon to occur from carbon-rich austenite, which results in a high-carbon (high strength) martensite after transformation. Transformation to high strength martensite continues as deformation increases, as long as retained austenite is still available to be transformed.
Alloys capable of the TRIP effect are characterized by a high ductility – high strength combination. Such alloys include 1st Gen AHSS TRIP steels , as well as several 3rd Gen AHSS grades like TRIP-Assisted Bainitic Ferrite, Carbide Free Bainite, and Quench & Partition Steels .
Back to the Top
Talk Like a Metallurgist
More Reveals of the Steel E-Motive Autonomous Vehicle Demonstration
What are 3rd Gen AHSS?
Conventional Rule-of-Thumb Calculations Lead to Inaccurate Press Tonnage Predictions
A New Global Formability Diagram
Press Hardened Steels
> View Steel Grades

- Search this website
- Useless Information about materials
- Why we need strong materials
- The Metal Men
- Sustainable Metallurgy
- Goals of Sustainable Metallurgy
- Sustainable Metals for the Energy Transition
- Carbon Footprint of Green Steel
- The Green Steel Deal
- Green Steel: the role of scrap
- Pellets for Hydrogen-Based Green Steel Making
- Green Steel: Direct reduction of iron ore with hydrogen
- Green Steel: Reduction of iron ore by hydrogen plasma
- Simulation of Hydrogen-based direct reduction
- Combining direct and plasma reduction
- Sustainable steel production: Strip casting of steel
- Green steel making with ammonia
- What is red mud and why is it dangerous?
- Sustainable metals for electromobility
- Green Aluminium
- Making Aluminium from Scrap
- EBSD and 3D EBSD
- Digital Image Correlation DIC
- Digital Image Correlation for multiphase alloys
- Digital Image Correlation and crystal plasticity simulation
- Dissipative deformation heating
- Atom probe tomography
- Atom probe tomography cryogenic UHV prep
- Atom probe and atomistic simulations
- Correlative atom probe tomography
- Atom probe tomography on steels
- Atom probe tomography on metallic glass
- Field Ion Microscopy - Mapping single atoms
- Crystallographic Textures
- Grain boundary segregation engineering
- Multiscale modeling
- Ab initio modeling
- DDD: Discrete dislocation dynamics
- Shear banding
- Linear Complexions
- Nanoindentation and pillar compression
- Indentation pile-up
- Recrystallization and grain growth simulation
- Constitutive modeling
- Chemistry dependence of constitutive models
- Crystal Plasticity Finite Element Method
- Dislocation-based Crystal Plasticity Finite Element Method
- Polycrystal mechanics
- RVE and homogenization simulation
- Sheet forming simulation
- Yield Surface Simulation
- Large scale crystal plasticity amd ansiotropy simulation
- Phase field and Ginzburg-Landau modeling
- Joint crystal plasticity and phase field models
- Lattice Boltzmann model (LBM)
- Steels: Brief introduction
- Steels: facts, figures, environment
- Bainite steels
- Martensite alloys and transformations
- Pearlitic steels
- QP - Quench - partitioning steels
- TRIPLEX steels
- Electrical steels (Fe-3%Si)
- Soft magnetic alloys
- Non-Oriented Electrical Steels
- Soft magnetic steels for electromobility
- ODS Eurofer steels
- Nanolaminates
- Nanolaminate steels
- Steels for additive manufacturing
- Dual phase steels
- Medium Mn steels
- Hydrogen and hydrogen embrittlement
- Hydrogen embrittlement of medium Mn steel
- Stainless steels
- Combinatorial steel design
- Ultrafine grained steels
- Textures of Steels
- Textures of dual phase steels
- Metallurgical Alloy Design
- Metastability Alloy Design
- TWIP steels
- TRIP steels
- Shape Memory Steels
- Combining TWIP and TRIP
- Low density and weight reduced steels
- High stiffness steels
- Iron-Aluminides
- High strength composites
- Thermoelectric half-Heusler alloys
- Magnesium alloys
- Magnesium applications
- Copper alloys and Copper-Nano-Composites
- Aluminium alloys
- Aluminium alloys for aerospace applications
- High Entropy Alloys - Overview
- Metastable High Entropy Alloys
- Non-Equiatomic High Entropy Alloys
- TWIP High Entropy Alloys
- Dual Phase High Entropy Alloys
- High Entropy Alloys and Hydrogen
- Interstitial High Entropy Alloys
- High Entropy Alloys by Text Mining
- High Entropy Steels
- Bi-directional TRIP High Entropy Alloys
- Medium Entropy Alloys
- Combinatorial discovery of high-entropy alloys
- Titanium alloys
- Nickel Alloy 718
- Superalloys
- Cobalt Alloys
- Multilayer Nitride Coatings
- Important Alloy Classes
- Bauschinger Effect
- Laser Additive Manufacturing
- Additive Manufacturing with Steel
- Segregation Engineering in Additive Manufacturing
- Welding Microstructures
- Seminconductors Solar Cells
- Biological (natural) Materials
- Chitin structure
- Hierarchical Architecture of Chitin
- Polymer Materials
- Dramatic material failure
- Movies and Animations
- RSS feeds MSE Journals
- Steel properties and overview Images
- Materials Science Image Gallery
- Large projects
- History of materials
- Useful links
- Infos for Materials Scientists
- Basic structure information on metals
- Glossary of materials science
- Cantus Mirabilis
- Metals in poetry
- Science cartoons
- Animated gifs for science
- Max-Planck-Institut
- Scientific CV
- Journal publications
- Review publications
- Research projects
Transformation Induced Plasticity Steels - TRIP steels
What is a trip effect .
The TRIP effect is the particular formation of martensite induced by forming. Here, the stress-induced formation of martensite must be distinguished from the deformation-induced formation of martensite, since the TRIP effect only sets in with the latter. This causes a simultaneous increase in hardness and formability under plastic stress in product manufacture or use. The extent of the effect is mainly influenced by the inexpensive alloying elements carbon, manganese, aluminium and silicon.
The material's own yield strength is higher than that of comparable steels, as the added silicon allows solid solution hardening. As soon as the plastic range is reached during forming or deformation, the metastable carbon-rich austenite begins to transform into martensite induced by deformation. As a result, the TRIP steel is specifically hardened by the plastic deformation.
Microstructure of TRIP steels
The microstructure of Transformation-Induced Plasticity (TRIP) steels contains retained austenite embedded in a matrix of ferrite, bainite or martensite depending on alloy composition and preceding processing.
Also mixtures of these matrix compunds are frequently used. TRIP steels are typically hypoeutectoid iron carbon alloys often with 0.1 – 0.4 mass% carbon. The metastable austenite is typcially in the form of retained and partitioned austenite but reversed auistenite can be used too. Typically TRIP steels contain 5-10 vol.% of metastable retained austenite or sometimes more.
Upon mechanical loading TRIP steels first undergo conventional dislocation plasticity of the soft ferrite portions of the microstructures and with further increase in deformation the retained austenite fraction progressively
transforms into martensite, thereby increasing the work hardening rate at higher strain levels.
What is spectral TRIP and how does it enable 1.1 GPa alloys?
Introduction of interlath reverted austenite is an effective method to design ductile lath martensitic steels. The challenge in this concept is that all reverted austenite films have similar mechanical stability, hence, they all undergo transformation-induced plasticity (TRIP) at the same strain level. Here we propose a new thermo-mechanical treatment route to activate the TRIP effect over a broad strain regime and refer to it as ‘spectral TRIP effect’. It aims at spreading the micro-mechanical stability of reverted austenite grains by widening the austenite nucleation barrier in martensite. To validate the proposed thermo-mechanical treatment route, an as-quenched medium-Mn martensitic steel was cold rolled prior to the reversion treatment at 600 C. Microstructure characterization was carried out by electron backscatter diffraction (EBSD) and electron channeling contrast imaging (ECCI). Mechanical tests show that the approach is effective. The spectral TRIP effect improves both, the strength and the ductility due to the well dispersed size distribution and the associated size-dependent deformation and phase transformation behavior of the reverted austenite grains, extending TRIP-related work hardening over a broad strain range.

TRIP effect in Medium-Manganese Steels
In this project the effects of prior austenite (gamma) grain boundaries and microstructural morphology on the impact toughness of an annealed Fe-7Mn-0.1C-0.5Si medium Mn steel were investigated for two different microstructure states, namely, hot-rolled and annealed (HRA) specimens and cold-rolled and annealed (CRA) specimens. Both types of specimens had a dual-phase microstructure consisting of retained austenite (gamma-R) and ferrite (a) after intercritical annealing at 640°C for 30 min. The phase fractions and the chemical composition of retained austenite were almost identical in both types of specimens. However, their microstructural morphology was different. The HRA specimens had lath-shaped morphology and the CRA specimens had globular-shaped morphology. We find that both types of specimens showed transition in fracture mode from ductile and partly quasi-cleavage fracture to intergranular fracture with decreasing impact test temperature from room temperature to 196°C. The HRA specimen had higher ductile to brittle transition temperature and lower low-temperature impact toughness compared to the CRA specimen. This was due to intergranular cracking in the HRA specimens along prior gamma grain boundaries decorated by C, Mn and P. In the CRA specimen intergranular cracking occurred along the boundaries of the very fine a and a' martensite grains. The results reveal that cold working prior to intercritical annealing promotes the elimination of the solute-decorated boundaries of coarse prior gamma grains through the recrystallization of aʹ martensite prior to reverse transformation, hence improving the lowtemperature impact toughness of medium Mn steel.

How can we design TRIP steels with core-shell microstructures?
The mechanical performance of multi-phase steel microstructures critically depends on the constituents’ chemical and morphological constitutions, which in combination determine the composite hardness, the onset of plasticity, internal load and strain-partitioning, as well as the stability and transformation kinetics of retained austenite in case of TRIP steels. The novel approach of utilising temporary vessel phases, hence termed vessel microstructure design, enables the tuning of constituent phase properties by linking their formation to a controllable landscape of chemical gradients. This approach hinges on the introduction of alloy carbides as a temporary container, or ‘vessel’ phase, deliberately producing localised enrichment of alloying elements in a structure predetermined by preliminary heat treatments, referred to as conditioning and accumulation stages. These vessel carbides, which act as reservoirs for specific alloying elements, are then partially dissolved through flash heating, leading to a self-organising landscape of alloying elements in the vicinity of the dissolving particles. The resulting three- or multiple phase microstructures then consist of confined laminates incorporating retained carbides, enveloped by retained austenite shells, embedded within a martensitic matrix. Such complex yet entirely self-organized microstructures offer unique opportunities for strain and load partitioning which we refer to as core-shell micromechanics. Different variants of these core-shell composite structures are produced and examined together with reference microstructures by tensile testing, hardness mappings, impact toughness, X-ray measurements, as well as by electron microscopy. It is found that these novel microstructures, when tempered, exhibit ultra-high strength and delayed necking, enabled by a combination of gradual strain-hardening and transformation-induced plasticity that is tuneable via control of the initial carbide structure.
Which crystallographic orientation relationships matter during transformation of austenite to bainite in TRIP steels?
The crystallographic orientation relationships that are active during the transformation of austenite to bainite are studied for two TRIP steels by means of Electron BackScatter Diffraction (EBSD). A detailed evaluation of about 360 retained austenite grains and their BCC neighbours was performed. Three relationships were considered, namely Kurdjumov–Sachs, Nishiyama–Wassermann and Pitsch. It was found that the majority of the austenite grains had at least one neighbour that could be related with one of the three orientation relationships. The Kurdjumov–Sachs relationship appeared to be dominant and no strong indication for variant selection could be retrieved from the studied data. It was, however, also demonstrated that some precautions need to be made since a clear distinction between the evaluation of a small region of the microstructure and conclusions made for the complete material is necessary.
Transformation-induced plasticity–twinning-induced plasticity steel with high damage resistance
Conventional martensitic steels have limited ductility due to insufficient microstructural strain-hardening and damage resistance mechanisms. It was recently demonstrated that the ductility and toughness of martensitic steels can be improved without sacrificing the strength, via partial reversion of the martensite back to austenite. These improvements were attributed to the presence of the transformation-induced plasticity (TRIP) effect of the austenite phase, and the precipitation hardening (maraging) effect in the martensitic matrix. However, a full micromechanical understanding of this ductilizing effect requires a systematic investigation of the interplay between the two phases, with regards to the underlying deformation and damage micromechanisms. For this purpose, in this work, a Fe–9Mn–3Ni–1.4Al–0.01C (mass%) medium-Mn TRIP maraging steel is produced and heat-treated under different reversion conditions to introduce well-controlled variations in the austenite–martensite nanolaminate microstructure. Uniaxial tension and impact tests are carried out and the microstructure is characterized using scanning and transmission electron microscopy based techniques and post mortem synchrotron X-ray diffraction analysis. The results reveal that (i) the strain partitioning between austenite and martensite is governed by a highly dynamical interplay of dislocation slip, deformation-induced phase transformation (i.e. causing the TRIP effect) and mechanical twinning (i.e. causing the twinning-induced plasticity effect); and (ii) the nanolaminate microstructure morphology leads to enhanced damage resistance. The presence of both effects results in enhanced strain-hardening capacity and damage resistance, and hence the enhanced ductility.
How to model twinning- and transformation-induced plasticity? A crystal plasticity approach.
Here a dislocation density-based crystal plasticity model incorporating both transformation-induced plasticity (TRIP) and twinning-induced plasticity (TWIP) is presented. The approach is a physically-based model which reflects microstructure investigations of ε-martensite, twins and dislocation structures in high manganese steels. Validation of the model was conducted using experimental data for a TRIP/TWIP Fe- 22Mn-0.6C steel. The model is able to predict, based on the difference in the stacking fault energies, the activation of TRIP and/or TWIP deformation mechanisms at different temperatures.
Is there a size effect in TRIP steels ?
Steels containing reverted nanoscale austenite islands or films dispersed in a martensitic matrix show excellent strength, ductility and toughness. The underlying microstructural mechanisms responsible for these improvements are not yet understood, but are observed to be strongly connected to the island or film size. Two main micromechanical effects are conceivable in this context, namely: (i) interaction of gamma with microcracks from the matrix (crack blunting or arresting); and (ii) deformation-induced phase transformation of gamma to martensite (TRIP effect). The focus here is on the latter phenomenon. To investigate size effects on gamma transformation independent of other factors that can influence austenite stability (composition, crystallographic orientation, defect density, surrounding phase, etc.), a model (TRIP-maraging steel) microstructure is designed with support from diffusion simulations (using DICTRA software) to have the same, homogeneous chemical composition in all gamma grains. Characterization is conducted by in-situ tension and bending experiments in conjunction with high-resolution electron backscatter diffraction mapping and scanning electron microscopy imaging, as well as post-mortem transmission electron microscopy and synchrotron X-ray diffraction analysis. Results reveal an unexpected “smaller is less stable” effect due to the size-dependent competition between mechanical twinning and deformation-induced phase transformation.
How to combine the TRIP effect with the maraging effect in one alloy class: TRIP-maraging steels
We present mechanical and microstructure results on precipitation-hardened ductile high-strength martensitic and austenitic–martensitic steels (up to 1.5 GPa strength) with good ductility. The alloys have a low-carbon content (0.01 wt.% C), 9–12 wt.% Mn, and minor additions of Ni, Ti and Mo (1–2 wt.%). Hardening is based on transformation-induced plasticity and the formation of intermetallic nanoprecipitates in the martensite during heat treatment (aging). The approach leads to an unexpected simultaneous increase in both strength and total elongation.
Can High Entropy Alloys have a TRIP effect?
In this project we developed a metastability-engineering strategy for the design of nanostructured, bulk high-entropy alloys with multiple compositionally equivalent high-entropy phases. High-entropy alloys were originally proposed to benefit from phase stabilization through entropy maximization. Yet here, motivated by recent work that relaxes the strict restrictions on high-entropy alloy compositions by demonstrating the weakness of this connection, the concept is overturned. We decrease phase stability to achieve two key benefits: interface hardening due to a dual-phase microstructure (resulting from reduced thermal stability of the high-temperature phase); and transformation-induced hardening (resulting from the reduced mechanical stability of the room-temperature phase). This combines the best of two worlds: extensive hardening due to the decreased phase stability known from advanced steels and massive solid-solution strengthening of high-entropy alloys3. In our transformation-induced plasticity-assisted, dual-phase high-entropy alloy (TRIP DP- HEA), these two contributions lead respectively to enhanced trans-grain and inter-grain slip resistance, and hence, increased strength. Moreover, the increased strain hardening capacity that is enabled by dislocation hardening of the stable phase and transformation-induced hardening of the metastable phase produces increased ductility.

How is the interplay of strain partitioning and chemcial partitioning in TRIP steel?
For studying the interplay of micromechanics and local composition partitioning among the neighboring phases we applied two types of hot-rolling direct quenching and partitioning (HDQ&P) schemes to a low-C low-Si Al-added steel and obtained two ferrite-containing TRIP-assisted steels with different hard matrix structures, viz, martensite or bainite. Using quasi in-situ tensile tests combined with high-resolution electron back-scattered diffraction (EBSD) and microscopic digital image correlation (m-DIC) analysis, we quantitatively investi- gated the TRIP effect and strain partitioning in the two steels and explored the influence of the strain partitioning between the soft and hard matrix structures on the TRIP effect. We also performed an atomic-scale analysis of the carbon partitioning among the different phases using atom probe tomography (APT) . The results show that the strain mainly localizes in the ferrite in both types of materials. For the steel with a martensitic hard-matrix, a strong strain contrast exists between ferrite and martensite, with the local strain difference reaching up to about 75% at a global strain of 12.5%. Strain localization bands initiated in the ferrite rarely cross the ferrite/martensite interfaces. The low local strain (2%-10%) in the martensite regions leads to a slight TRIP effect with a transformation ratio of the retained austenite of about 7.5%. However, for the steel with bainitic matrix, the ferrite and bainite undergo more homogeneous strain partitioning, with an average local strain in ferrite and bainite of 15% and 8%, respectively, at a global strain of 12.5%. The strain localization bands originating in the ferrite can cross the ferrite/bainite (F/B) interfaces and increase the local strain in the bainite regions, resulting in an efficient TRIP effect. In that case the transformation ratio of the retained austenite is about 41%. The lower hardness difference between the ferrite and bainite of about 178 HV, compared with that between the ferrite and martensite of about 256 HV, leads to a lower strain contrast at the ferrite/bainite interfaces, thus retarding interfacial fracture. Further microstructure design for TRIP effect optimization should particularly focus on adjusting the strength contrast among the matrix structures and tuning strain partitioning to enhance the local strain partitioning into the retained austenite.

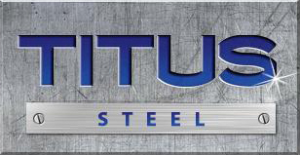
- Send us an Email [email protected]
- Everything You Need to Know about Endura Steel’s “TRIP EFFECT”
- Titus Steel
- posted by: Titus Steel
- March 9, 2020
- No Comments
TRIP refers to “TRANSFORMATION INDUCED PLASTICITY” and is sometimes referred to as TRIP STEELS. With TRIP, the steel undergoes a slow transformation when stress and/or deformation is applied to the steel. For example, in applications of severe impact abrasion .
How does ENDURA Steel’s TRIP Work?
Austenite, which remained after heat treatment, is transformed to Martensite thereby increasing the strength, ductility and overall hardness of the steel. In other words, the more the steel is hit, compressed or impacted, the harder it gets and, most importantly, the more ductile it becomes.
Think of catching a baseball. You hold your hand in a ridged position and the ball crashes into, and damages your hand. Now imagine letting your hand “give a little” as you catch the ball, like a trampoline. A great reduction in the damage to your hand would be seen.
This is the TRIP EFFECT of ENDURA and ENDURA DUAL when rocks, gravel and other abrasive materials crash into it, and is why it out lasts all other wear steels.
Is TRIP Exclusive to Endura Steel?
ENDURA and ENDURA Dual are the only wear steels with TRIP EFFECT.
Because of the trip effect, chemistry, and homogeneous microstructure ENDURA and ENDURA Dual will outlast other wear steels. This means less downtime, and in some cases, a reduction in steel thickness enabling an increase in payload.
To learn more about the ENDURA and ENDURA Dual advantage, visit our ENDURA Steel product page . You can also contact us today , and we’ll help you to find the best steel to meet your needs.
Advertisement
TRIP effect produced by cold rolling of austenitic stainless steel AISI 316L
- Metals & corrosion
- Published: 03 February 2023
- Volume 58 , pages 3334–3345, ( 2023 )
Cite this article
- Ricardo Luiz Perez Teixeira ORCID: orcid.org/0000-0003-2641-4036 1 ,
- José Carlos de Lacerda 1 ,
- Kevinny Chaves Florencio 1 ,
- Sidney Nicodemos da Silva 2 &
- Andréia Bicalho Henriques 3
594 Accesses
2 Citations
Explore all metrics
This study aims to study the transformation-induced plasticity (TRIP) by cold rolling in AISI 316L grade ASTM F138: 2019 (biomedical material) and its compliance with ISO 5832. The cold rolling of 316L is less expensive and gives a good surface finish and dimensional deviations as compared with casting, powder metallurgy, additive manufacturing, and forging. However, the cold working processes of 316L stainless steel can produce unwanted phases by the TRIP effect that limits its use as a biomaterial according to ISO. Understanding the TRIP effect of 316L by cold rolling can help to become more accessible to biomedical engineering applications. To evaluate the TRIP effect on cold-rolled 316L steel under conditions of low thickness reduction (deformation) of 10, 20, and 30%, mechanical, electrochemical, morphological, magnetic, and crystallographic analyses were performed. Crystallographic analysis by X-ray diffractograms indicated the presence of martensitic crystalline phase α’ for samples with 20 and 30% thickness reduction, which was also verified by metallographic, Vickers microhardness, and ferritoscopy tests. Based on the results obtained, the reversion treatment is recommended for cold conformations in 316L steel as a metallic biomaterial greater than 10% thickness reduction.
This is a preview of subscription content, log in via an institution to check access.
Access this article
Subscribe and save.
- Get 10 units per month
- Download Article/Chapter or eBook
- 1 Unit = 1 Article or 1 Chapter
- Cancel anytime
Price includes VAT (Russian Federation)
Instant access to the full article PDF.
Rent this article via DeepDyve
Institutional subscriptions
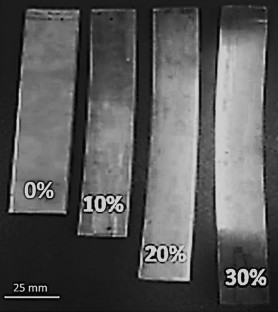
Similar content being viewed by others
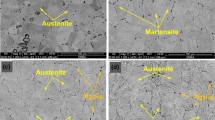
Role of Effective Strain During Cold Rolling Deformation on Mechanical Characteristics of AISI 304 Steel
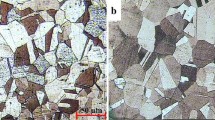
The Effect of Cold Rolling on Microstructure and Mechanical Properties of a New Cr–Mn Austenitic Stainless Steel in Comparison with AISI 316 Stainless Steel
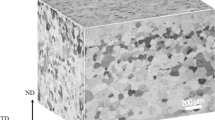
Influence of Cold Rolling on the Recrystallization Texture and Ridging of AISI 430 Type Ferritic Stainless Steel
Explore related subjects.
Pires ALR, Bierhalz ACK, Moraes AM (2015) Biomaterials: types, applications, and market. Química Nova 38: 957–971. https://www.scielo.br/scielo.php?script=sci_arttext&pid=S0100-40422015000700957 .
Marques AVM, Carmo KMD, Lage WC, Teixeira RLP, Lacerda JCD, Teixeira CHSB, Shitsuka R (2020) Evaluation of the effect of plastic deformation on the microstructure, hardness and magnetic properties of AISI type 316L stainless steel. Matéria (Rio de Janeiro) 25. https://www.scielo.br/j/rmat/a/BMPfCmgcbyW97vTNMLD7GJG/?lang=pt .
Pathote D, Jaiswal D, Singh V, Behera CK (2022) Optimization of electrochemical corrosion behavior of 316L stainless steel as an effective biomaterial for orthopedic applications. Mater Today proc 57:265–269. https://doi.org/10.1016/j.matpr.2022.02.501
Article CAS Google Scholar
ASTM F139-12. Standard Specification for Wrought 18Chromium-14Nickel-2.5Molybdenum Stainless Steel Sheet and Strip for Surgical Implants (UNS S31673) (2012). https://www.astm.org/f0139-12.html
He B (2020) On the factors governing austenite stability: intrinsic versus extrinsic. Materials 13(15):3440. https://doi.org/10.3390/ma13153440
Sohrabi MJ, Mirzadeh H, Dehghanian C (2020) Microstructure and mechanical properties of cold rolled AISI 304L and 316L austenitic stainless steels during reversion annealing. Iran J Mater Forming 7(1):92–99. https://ijmf.shirazu.ac.ir/article_5744_03ed43392306bbe6fd08c3b03193843f.pdf
Bleck W, Guo X, Ma Y (2017) The TRIP effect and its application in cold formable sheet steels. Steel Res Int 88(10):1700218. https://doi.org/10.1002/srin.201700218
ISO 5832-1. Implants for surgery—metallic materials—Part 1: Wrought stainless steel, International Organization for Standardization (2016) https://www.iso.org/standard/66636.html
Asri RIM, Harun WSW, Samykano M, Lah NAC, Ghani SAC, Tarlochan F, Raza MR (2017) Corrosion and surface modification on biocompatible metals: a review. Mater Sci Eng C 77:1261–1274. https://doi.org/10.1016/j.msec.2017.04.102
ASTM F138-19. Standard specification for wrought 18Chromium-14Nickel-2.5Molybdenum stainless steel bar and wire for surgical implants (UNS S31673) (2019). https://www.astm.org/f0138-19.html
Ratner BD, Hoffman AS, Schoen FJ, Lemons JE (2004) Biomaterials science: an introduction to materials in medicine. San Diego, California, pp. 162–4. https://www.cambridge.org/core/journals/mrs-bulletin/article/library/0D723BFF0B9D79E2BE31A292CF83D973
Marques RA, Rogero SO, Terada M, Pieretti EF, Costa I (2014) Localized corrosion resistance and cytotoxicity evaluation of ferritic stainless steels for use in implantable dental devices with magnetic connections. Int J Electrochem Sci 9(3):1340. http://www.electrochemsci.org/papers/vol9/90301340.pdf
MARKET DATA (2021) Global Biomaterials Market Size, Share, Trends, COVID-19 Impact & Growth Analysis Report—Segmented by Material Type, Application and Region—Industry Forecast (2021 to 2026) (2021). https://www.marketdataforecast.com/market-reports/biomaterials-market
THE EMERGEN RESEARCH. Biomaterials Market by Type (Ceramic, Metallic, Polymeric, Natural, Others), By Application (Cardiovascular, Ophthalmology, Orthopedic, Plastic Surgery, Neurology, Others), and Regions Forecasts to 2027 (2020) https://www.emergenresearch.com/industry-report/biomaterialsmarket
Callister Jr WD, Rethwisch DG (2021) Fundamentals of materials science and engineering: an integrated approach. Wiley, New York. https://www.wiley.com/en-br/Fundamentals+of+Materials+Science+and+Engineering%3A+An+Integrated+Approach%2C+6th+Edition-p-9781119688945
Staiger MP, Pietak AM, Huadmai J, Dias G (2006) Magnesium and its alloys as orthopedic biomaterials: a review. Biomaterials 27(9):1728–1734. https://doi.org/10.1016/j.biomaterials.2005.10.003
Sumita M, Hanawa T, Teoh SH (2004) Development of nitrogen-containing nickel-free austenitic stainless steels for metallic biomaterials. Mater Sci Eng C 24(6–8):753–760. https://doi.org/10.1016/j.msec.2004.08.030
Hanawa T (2004) Metal ion release from metal implants. Mater Sci Eng C 24(6–8):745–752. https://doi.org/10.1016/j.msec.2004.08.018
Davis JR (2003) Handbook of materials for medical devices, 1st edn. ASM International, USA. https://www.asminternational.org/documents/10192/1849770/06974G_Frontmatter.pdf
Al-Rashidy ZM, Farag MM, Ghany NA, Ibrahim AM, Abdel-Fattah WI (2018) Orthopedic bioactive glass/chitosan composites coated 316L stainless steel by green electrophoretic co-deposition. Surf Coat Technol 334: 479–490. https://doi.org/10.1016/j.surfcoat.2017.11.052
Prasad K, Bazaka O, Chua M et al (2017) Metallic biomaterials: current challenges and opportunities. Mater 10(8):884. https://doi.org/10.3390/ma10080884
Teixeira RLP, de Lacerda JC, Conceição IC, da Silva SN, Siqueira GO, Moura Filho F (2021) The effects of Niobium on the bioactivity of Ni-Ti-al-Nb shape memory alloys. Arch Metallurgy Mater 66(2). https://doi.org/10.24425/amm.2021.135876
Aksakal B, Yildirim ÖS, Gul H (2004) Metallurgical failure analysis of various implant materials used in orthopedic applications. J Failure Anal Prevent 4(3):17–23. https://doi.org/10.1007/s11668-996-0007-9
Hosseini MR, Ahangari M, Johar MH, Allahkaram SR (2021) Optimization of nano HA-SiC coating on AISI 316L medical grade stainless steel via electrophoretic deposition. Mater Lett 285:129097. https://doi.org/10.1016/j.matlet.2020.129097
Tümer D, Güngörürler M, Havıtçıoğlu H, Arman Y (2020) Investigation of effective coating of the Ti–6Al–4V alloy and 316L stainless steel with graphene or carbon nanotubes with finite element methods. J Mater Res Technol 9(6):15880–15893. https://doi.org/10.1016/j.jmrt.2020.11.052
Vafa E, Bazargan-Lari R, Bahrololoom ME (2021) Electrophoretic deposition of polyvinyl alcohol/natural chitosan/bioactive glass composite coatings on 316L stainless steel for biomedical application. Progress Organic Coatings 151:106059. https://doi.org/10.1016/j.porgcoat.2020.106059
Kaur S, Bala N, Khosla C (2019) Characterization of hydroxyapatite coating on 316L stainless steel by sol–gel technique. Surf Eng Appl Electrochem 55(3):357–366. https://doi.org/10.3103/S1068375519030104
Rivlin VG, Raynor GV (1980) 1: Critical evaluation of constitution of chromium-iron-nickel system. Int Metals Rev 25(1):21–40. https://doi.org/10.1179/imtr.1980.25.1.21
Stewart BWKP, Christopher PW (2014) International agency for research on cancer. World cancer report 2014. https://publications.iarc.fr/Non-Series-Publications/World-Cancer-Reports/World-Cancer-Report-2014
Sohrabi MJ, Naghizadeh M, Mirzadeh H (2020) Deformation-induced martensite in austenitic stainless steels: a review. Arch Civil Mech Eng 20(4):1–24. https://doi.org/10.1016/j.vacuum.2018.08.066
Soleimani M, Kalhor A, Mirzadeh H (2020) Transformation-induced plasticity (TRIP) in advanced steels: a review. Mater Sci Eng A 795: 140023. https://doi.org/10.1016/j.msea.2020.140023
Santos DB, Barbosa R, de Oliveira PP, Pereloma EV (2009) Mechanical behavior and microstructure of high carbon Si–Mn–Cr Steel with trip effect. ISIJ Int 49(10):1592–1600. https://doi.org/10.2355/isijinternational.49.1592
Zackay VF, Parker ER, Fahr D, Busch R (1967) The enhancement of ductility in high-strength steels. ASM Trans Quart 60(2):252–259. https://jglobal.jst.go.jp/en/detail?JGLOBAL_ID=201602018455359736
Bleck W, Xiaofei G, Ma Y (2017) The TRIP effect and its application in cold formable sheet steels. Steel Res Int 88(10):1700218. https://doi.org/10.1002/srin.201700218
Wei Y, Lu Q, Kou Z, Feng T, Lai Q (2023) Microstructure and strain hardening behavior of the transformable 316L stainless steel processed by cryogenic pre-deformation. Mater Sci Eng A 862:144424. https://doi.org/10.1016/j.msea.2022.144424
Leslie WC (1981) The physical metallurgy of steels. Hemisphere Publishing Corp., London, pp 396. https://lib.ugent.be/catalog/rug01:000436817
ASTM E112-13. Standard Test Methods for Determining Average Grain Size (2021). https://www.astm.org/e0112-13r21.html
Ashby MF, Shercliff H, Cebon D (2018) Materials: engineering, science, processing and design. Butterworth-Heinemann, UK. https://shop.elsevier.com/books/materials/ashby/978-0-08-102376-1
Sabooni S, Karimzadeh F, Enayati MH, Ngan AHW, Jabbari H (2015) Gas tungsten arc welding and friction stir welding of ultrafine grained AISI 304L stainless steel: microstructural and mechanical behavior characterization. Mater Characterization 109:138–151. https://doi.org/10.1016/j.matchar.2015.08.009
Padilha AF, de Aguiar DJM, Plaut RL (2012) Duplex stainless steels: a dozen of significant phase transformations. Defect and diffusion forum. Vol. 322. Trans Tech Publications Ltd. https://doi.org/10.4028/www.scientific.net/DDF.322.163
Marques FM, Rocha ADS, Santos GR, Wolfart Junior M, Costa RC, Ferreira JZ (2021) The influence of surface condition on the electrochemical properties of ASTM F138 steel for biomedical applications. Mater Res 24. https://doi.org/10.1590/1980-5373-MR-2020-0062
Padilha AF, Ronald LP, Rios PR (2003) Annealing of cold-worked austenitic stainless steels. ISIJ Int 43(2):135–143. https://doi.org/10.2355/isijinternational.43.135
Diniz AE, Machado AR, Corrêa JG (2016) Tool wear mechanisms in the machining of steels and stainless steels. Int J Adv Manufact Technol 87(9):3157–3168. https://doi.org/10.1007/s00170-016-8704-3
Article Google Scholar
Berrahmoune MR, Berveiller S, Inal K, Patoor K (2006) E Delayed cracking in 301LN austenitic steel after deep drawing: martensitic transformation and residual stress analysis. Mater Sci Eng A 438:262–266. https://doi.org/10.1016/j.msea.2006.02.189
Sandim MJR, Mauro V, Tavares SSM, Zilnyk KD, Sandim HRZ (2021) Magnetic properties and microstructural characterization of cold-rolled and annealed 317L austenitic stainless steel. J Magnet Magnet Mater 539:168336. https://doi.org/10.1016/j.jmmm.2021.168336
Altan T, Tekkaya AE (2012) Sheet metal forming: fundamentals. ASM International, USA. https://www.asminternational.org/documents/10192/1849770/05340G_TOC.pdf
Liverani E, Toschi S, Ceschini L, Fortunato A (2017) Effect of selective laser melting (SLM) process parameters on microstructure and mechanical properties of 316L austenitic stainless steel. J Mater Process Technol 249:255–263. https://doi.org/10.1016/j.jmatprotec.2017.05.042
ASTM E92–17(2017) Standard Test Methods For Vickers Hardness And Knoop Hardness Of Metallic Materials. https://webstore.ansi.org/standards/astm/astme9217
Nnakwo KC, Osakwe FO, Ugwuanyi BC, Oghenekowho PA, Okeke IU, Maduka EA (2021) Grain characteristics, electrical conductivity, and hardness of Zn-doped Cu–3Si alloys system. SN Appl Sci 3(11):1–10. https://doi.org/10.1007/s42452-021-04784-1
Li X, Cui L, Li J, Chen Y, Han W, Shonkwiler S, McMains S (2022) Automation of intercept method for grain size measurement: a topological skeleton approach. Mater Des 224:111358. https://doi.org/10.1016/j.matdes.2022.111358
IMAGEJ. Intersect Count Method for quantitative metallography (2022). https://imagej.nih.gov/ij/macros/toolsets/Intersects_Method.txt
Chadha K, Tian Y, Spray JG, Aranas C Jr (2020) Effect of annealing heat treatment on the microstructural evolution and mechanical properties of hot isostatic pressed 316L stainless steel fabricated by laser powder bed fusion. Metals 10(6):753. https://doi.org/10.3390/met10060753
Lacerda JCD, Freitas LLD., Brito RF, Moura Filho F, Teixeira RLP (2021) Comparative study between sensitization degree of the 0.4% Mo austenitic stainless steel and UNS S31803 duplex stainless steel. Mater Res 24.1:e20200408. https://doi.org/10.1590/1980-5373-MR-2020-0408 .
Lacerda JCD, Teixeira RLP, Souza, RMRD, Soares RB, Lins VDFC (2020) Pitting corrosion behavior of UNS S31803 and UNS S32304 duplex stainless steels in 3.5 wt% NaCl solution. Mater. (Rio de Janeiro) 25.2:e-12622. https://doi.org/10.1590/S1517-707620200002.1022
Teixeira RLP, de Lacerda JC, Conceição IC, da Silva S N, Siqueira GO, Moura Filho F (2021) The effects of niobium on the bioactivity of Ni-Ti-al-Nb shape memory alloys. Arch Metall Mater 66.2:437–442. http://imim.pl/files/archiwum/Vol2_2021/12.pdf
TESCAN VEGA (2022) Analytical SEM for routine materials characterization, research and quality control applications at the micron scale. https://www.tescan.com/product/sem-for-materials-science-tescan-vega/
Camerini CG, Silva VMA, Soares IA, Santos RWF, Ramos JE, Santos JMC, Pereira GR (2018) Ferrite content meter analysis for delta ferrite evaluation in superduplex stainless steel. J Market Res 7(3):366–370. https://doi.org/10.1016/j.jmrt.2018.06.005
Shahri MG, Salehi M, Hosseini SR, Naderi M (2017) Effect of nanostructured grains on martensite formation during plasma nitriding of AISI 321 austenitic stainless steel. Surf Coat Technol 310:231–238. https://doi.org/10.1016/j.surfcoat.2016.12.019
FERITSCOPE FMP30 (2022) Measurement of the Ferrite Content in Austenitic and Duplex Steel. https://www.qnde.ca/wp-content/uploads/2016/01/FERITSCOPE-FMP-30-catalogue.pdf
MALVERN PANALALYTICAL (2022) X-ray diffractometers, Benchtop & floorstanding XRD solutions. https://www.malvernpanalytical.com/en/products/category/x-ray-diffractometers
Sohrabi MJ, Mirzadeh H, Dehghanian C (2020) Significance of martensite reversion and austenite stability to the mechanical properties and transformation-induced plasticity effect of austenitic stainless steels. J Mater Eng Perform 29(5):3233–3242. https://doi.org/10.1007/s11665-020-04798-7
Kheiri S, Mirzadeh H, Naghizadeh M (2019) Tailoring the microstructure and mechanical properties of AISI 316L austenitic stainless steel via cold rolling and reversion annealing. Mater Sci Eng A 759:90–96. https://doi.org/10.1016/j.msea.2019.05.028
ICCD (2022) International Centre for Diffraction Data, Powder Diffraction File (PDF)—Phase Search. https://www.icdd.com/pdfsearch/
Singh R, Agrahari S, Yadav SD, Kumar A (2021) Microstructural evolution and mechanical properties of 316 austenitic stainless steel by CGP. Mater Sci Eng A 812: 141105. https://doi.org/10.1016/j.msea.2021.141105
Amininejad A, Jamaati R, Hosseinipour SJ (2019) Achieving superior strength and high ductility in AISI 304 austenitic stainless steel via asymmetric cold rolling. Mater Sci Eng A 767: 138433. https://doi.org/10.1016/j.msea.2019.138433
Zhou Z, Wang S, Li J, Li Y, Wu X, Zhu Y (2020) Hardening after annealing in nanostructured 316L stainless steel. Nano Mater Sci 2(1):80–82. https://doi.org/10.1016/j.msea.2021.141105
Silva EDF, Oliveira LFCD (2011) Chemical and metallographic characterization of stainless steel in implants removed from patients. Acta Ortopedica Brasileira 19:280–285. https://doi.org/10.1590/S1413-78522011000500003
Padilha AF, Rios PR (2002) Decomposition of austenite in austenitic stainless steels. ISIJ Int 42(4):325–327. https://doi.org/10.2355/isijinternational.42.325
Santos TA, Santos RCD, Martins WDP, Nascimento CCFD (2019) Avaliação da susceptibilidade à corrosão de um aço inoxidável AISI 316L submetido à simulação térmica com o uso da Gleeble. Matéria (Rio de Janeiro) 24. https://doi.org/10.1590/S1517-707620190003.0761
Lesyk DA, Soyama H, Mordyuk BN, Dzhemelinskyi VV, Martinez S, Khripta NI, Lamikiz A (2019) Mechanical surface treatments of AISI 304 stainless steel: effects on surface microrelief, residual stress, and microstructure. J Mater Eng Performance 28(9):5307–5322. https://doi.org/10.1007/s11665-019-04273-y
Download references
Author information
Authors and affiliations.
Federal University of Itajubá - Itabira Campus, Itabira, MG, 35900-000, Brazil
Ricardo Luiz Perez Teixeira, José Carlos de Lacerda & Kevinny Chaves Florencio
Federal Center for Technological Education of Minas Gerais, Belo Horizonte, MG, 30421-169, Brazil
Sidney Nicodemos da Silva
Federal University of Minas Gerais, Belo Horizonte, MG, 31270-901, Brazil
Andréia Bicalho Henriques
You can also search for this author in PubMed Google Scholar
Corresponding author
Correspondence to Ricardo Luiz Perez Teixeira .
Ethics declarations
Conflict of interest.
The authors declare that they have no conflict of interest.
Ethical approval
This research does not concern experiments involving humans and/or animals and does not require the approval of the ethics committee.
Additional information
Handling Editor: Catalin Croitoru.
Publisher's Note
Springer Nature remains neutral with regard to jurisdictional claims in published maps and institutional affiliations.
Rights and permissions
Springer Nature or its licensor (e.g. a society or other partner) holds exclusive rights to this article under a publishing agreement with the author(s) or other rightsholder(s); author self-archiving of the accepted manuscript version of this article is solely governed by the terms of such publishing agreement and applicable law.
Reprints and permissions
About this article
Teixeira, R.L.P., de Lacerda, J.C., Florencio, K.C. et al. TRIP effect produced by cold rolling of austenitic stainless steel AISI 316L. J Mater Sci 58 , 3334–3345 (2023). https://doi.org/10.1007/s10853-023-08235-7
Download citation
Received : 13 December 2022
Accepted : 21 January 2023
Published : 03 February 2023
Issue Date : February 2023
DOI : https://doi.org/10.1007/s10853-023-08235-7
Share this article
Anyone you share the following link with will be able to read this content:
Sorry, a shareable link is not currently available for this article.
Provided by the Springer Nature SharedIt content-sharing initiative
- Find a journal
- Publish with us
- Track your research
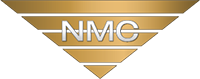
What are TRIP Steels?
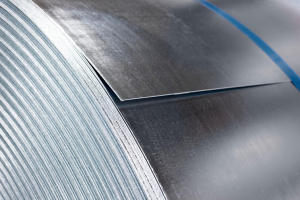
WHAT ARE TRIP STEELS (Transformation Induced Plasticity Steels)?
TRIP Steels (Transformation Induced Plasticity Steel) are part of the Advanced High-Strength Steel (AHSS) family.
The microstructure of TRIP steels consists of at least five-volume percent of retained austenite, which is embedded in a primary ferrite matrix. The microstructure also contains hard phases like bainite and martensite in varying amounts.
TRIP steels are notable due to the higher carbon content than other members of the AHSS family, such as dual phase steels. They typically require the use of an isothermal hold at an intermediate temperature, which produces some bainite. Silicon and aluminum are added in order to both accelerate the ferrite and bainite formation process, as well as avoiding carbide buildup in the bainite region of the material.
Greater silicon, aluminum, and carbon content of TRIP steels result in large fractions of retained austenite in the material’s final microstructure. The increased carbon content also stabilizes the retained austenite phase below the usual ambient temperature.
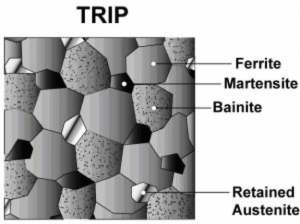
Changing the carbon content helps to control the strain level at which the austenite begins to transform into martensite. At low carbon levels, the transformation of the retained austenite will begin almost immediately upon deformation, which will then improve the formability and work hardening rate during the stamping process.
At higher carbon content, the transformation will occur only at strain levels beyond those utilized during the forming processing. The retained austenite remains after the final stage of the forming process at these higher carbon levels – the transformation into martensite will occur only during subsequent deformation; in the case of automobiles, an example would be a crash event.
PROPERTIES OF TRIP STEELS
TRIP Steels can be produced as hot-rolled, cold-rolled, or hot dip galvanized, with a strength range from 500 MPa to 800 MPa.
TRIP Steels are highly sought after due to their high work hardening rate, which is created by the hard second phases that are dispersed in the soft ferrite during deformation. Despite the fact that initial work hardening rate of the material is lesser than that of, say, dual phase steels, TRIP steels sustain their hardening rate at much higher strain levels, where DP steel’s work hardening rate would deteriorate.
As a result of the high work hardening rates, TRIP steels also have substantial stretch forming properties.
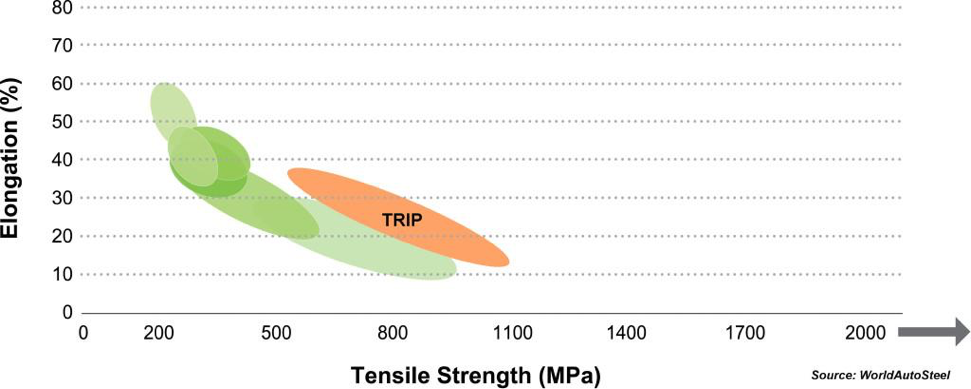
The high strain hardening capacity and mechanical strength make these steels an excellent candidate for automotive parts that require a high energy absorption capacity. TRIP steels also have a strong bake hardening following deformation, which even further improves their crash performance.
To summarize TRIP steel’s properties:
- Work hardening – When compared to other advanced high-strength steels, TRIP steels exhibit and retain a higher work hardening rate at higher levels of strain.
- Formability – As a byproduct of the high work hardening rate, these steels have substantial stretch forming properties, and can be put through stamping processes in a relatively stable manner.
- Bake hardening – TRIP steels have a very high bake hardening capacity, and can by doing so can increase their yield strength by close to 70 MPa.
- Product mass reduction capacity – Due to the above characteristics, these steels are good candidates for weight reduction and part down gauging techniques.
APPLICATION OF TRIP STEELS IN AUTOMOBILES
TRIP steels are excellent for automotive parts that require high work hardening during crash deformation and large amounts of energy absorption.
They are also very well-suited for creatingcomplicated, hard-to-form parts, which is a result of their high formability and work hardening attributes. Thus, they are handy for complex reinforcement and structural parts.
Current production grades of TRIP steels and example automotive applications:
TRIP 350/600 Frame rails, rail reinforcements
TRIP 400/700 Side rail, crash box
TRIP 450/800 Dash panel, roof rails
TRIP 600/980 B-pillar upper, roof rail, engine cradle, front and rear rails, seat frame
TRIP 750/980
About National Material L.P. – National Material Limited Partnership and its affiliates have a long history of quality and service dating back to 1964. Since its founding, National Material L.P. has grown to over 30 business units and is now one of the largest suppliers of steel in America. The National Material group of industrial businesses consists of the Steel Group, Stainless and Alloys Group, Raw Material Trading Group, Aluminum Group, and Related Operations.
Visit National Material: https://www.nationalmaterial.com or call (U.S.) 847-806-7200.
Share This Story, Choose Your Platform!
Related posts.
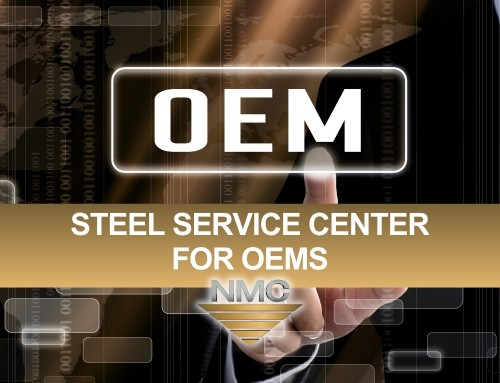
The Role of the Steel Service Center for OEMs
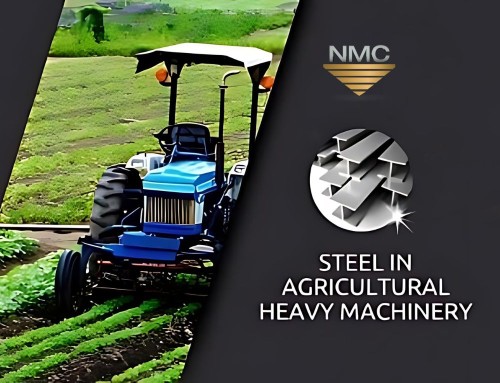

Why Use Steel in Agricultural Heavy Machinery
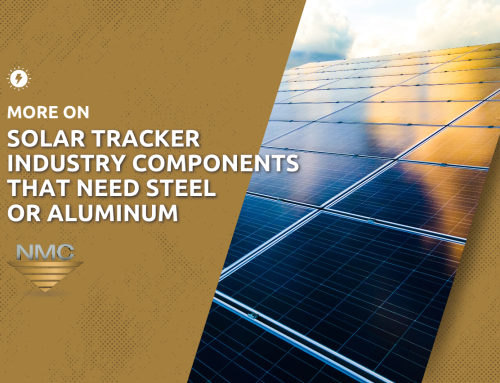
Solar Tracker Industry Components that Need Steel or Aluminum
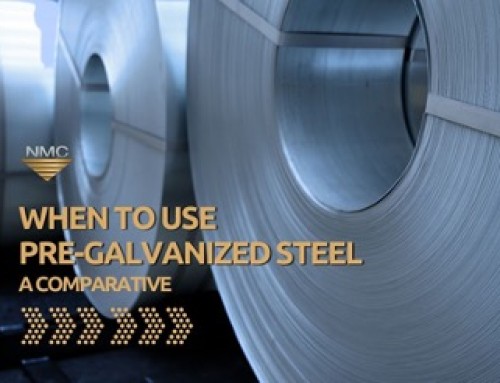
When to Use Pre-Galvanized Steel: A Comparative
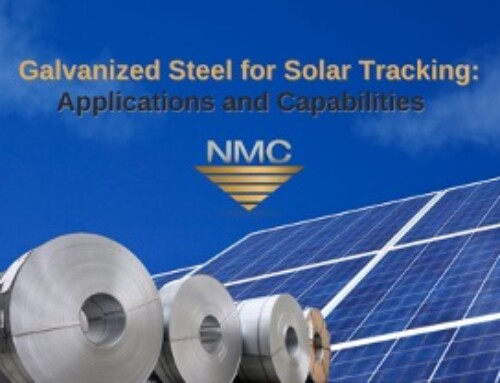
Galvanized Steel for Solar Tracking: Applications and Capabilities
Thank you for visiting nature.com. You are using a browser version with limited support for CSS. To obtain the best experience, we recommend you use a more up to date browser (or turn off compatibility mode in Internet Explorer). In the meantime, to ensure continued support, we are displaying the site without styles and JavaScript.
- View all journals
- My Account Login
- Explore content
- About the journal
- Publish with us
- Sign up for alerts
- Open access
- Published: 14 June 2021
Materials information and mechanical response of TRIP/TWIP Ti alloys
- Guohua Zhao ORCID: orcid.org/0000-0003-1737-2786 1 ,
- Xiaoqing Li ORCID: orcid.org/0000-0002-4322-7737 2 &
- Nik Petrinic 1
npj Computational Materials volume 7 , Article number: 91 ( 2021 ) Cite this article
4925 Accesses
22 Citations
1 Altmetric
Metrics details
- Computational methods
- Metals and alloys
Materials innovation calls for an integrated framework combining physics-based modelling and data-driven informatics. A dislocation-based constitutive model accounting for both transformation-induced plasticity (TRIP) and twinning-induced plasticity (TWIP) was built to interpret the mechanical characteristics of metastable titanium alloys. Particular attention was placed on quantitatively understanding the composition-sensitive phase stability and its influence on the underlying deformation mechanism. For this purpose, a pseudoelastic force balance incorporating thermodynamics and micromechanics was applied to calculate the energy landscapes of β → α ″ martensitic transformation, {332}〈113〉 twinning and dislocation slip. Extensive material data were probed, computed and fed to the model. Our results revealed that TRIP and TWIP may operate simultaneously because of the presence of a noticeably overlapped energy domain, and confirmed {332}〈113〉 twinning is an energetically favourable deformation mechanism. The model validation further unveiled that the activation of β → α ″ transition remarkably enhances the strain-hardening and plasticity, even though the dynamically formed α ″ volume fraction is much less than that of deformation twinning. Our work suggests that the synchronised physical metallurgy and data-driven strategy allows to identify the compositional scenarios for developing high-performance engineering alloys.
Similar content being viewed by others
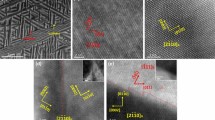
Transportation of dislocation plasticity in a dual-phase TiMo alloy
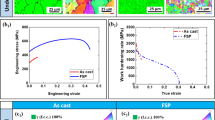
Co-introduction of precipitate hardening and TRIP in a TWIP high-entropy alloy using friction stir alloying
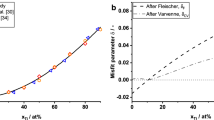
The influence of lattice misfit on screw and edge dislocation-controlled solid solution strengthening in Mo-Ti alloys
Introduction.
The aerospace sector plays a significant role in driving materials innovation 1 . Approximately one-third of the structural weight of modern turbine engines is made up of Ti alloys 2 , thanks to their excellent integrity of high specific strength, corrosion resistance and good stability to the elevated temperatures. Ti alloys with transformation-induced plasticity (TRIP) and/or twinning-induced plasticity (TWIP) effects have been showing superior toughness and ductility 3 . The enhanced damage-tolerance is especially important for the highest safety-critical aeroengine components, which is able to resist catastrophic crack growth and allows time for inspection. However, the TRIP/TWIP and TWIP Ti alloys are not fully exploited for engineering applications, and it requires a thorough understanding of the underlying deformation mechanisms. This necessitates a comprehensive strategy incorporating a selection of composition, microstructure and processing parameters to quantitatively capture the materials information and mechanical response. Here the term TRIP/TWIP designates simultaneous activation of strain-induced martensitic transformation and deformation twinning, whereas TWIP refers only twinning is operative.
The strain-transformable Ti alloys present excellent plasticity (i.e. uniform elongation (uEL)) via pronounced strain-hardening. For determining the property, it is critical to quantify the rate at which the critical stress evolves over strain or, equivalently, the rate at which dislocations accumulate under strain 4 . This is performed through modelling a key quantity, dislocation mean free path, which is the distance travelled by a dislocation segment before it is stored by the interaction with the microstructure features, such as dislocation forest. The mean free path is reduced as strain increase and may be interrupted by the transformation products of TWIP and TRIP. Furthermore, deformation twinning and martensitic transformation create extra shear to accommodate the strain increase. {332}〈113〉 twinning is a featured and widely exist twinning system in bcc (body-centred cubic) β Ti alloys, which produces \(\frac{1}{2\sqrt{2}}\) shear strain and the rest atoms are transferred by shuffling. Meanwhile, β phase may transform to α ″ martensite (C-orthorhombic) with the assistance of external load, and the crystal structure of α ″ is intermediate between bcc and hcp (hexagonal close packed). TRIP and TWIP deformation modes may undergo simultaneously because the mechanisms of martensitic transformation and deformation twinning are intrinsically analogous. A deformation twin is produced by a homogeneous shear of the lattice parallel to the twinning (habit) plane; whereas martensitic transformation occurs not only by a shear parallel to the habit plane, but also together with a small dilatation normal to the plane 5 . The analogy is also reflected on the dislocation mechanisms of martensite and twin nucleation. For instance in fcc (face-centred cubic) alloys, ε martensite nucleates by the arrangement of intrinsic stacking faults on every second {111} plane, whereas twins nucleates by overlapping three stacking faults on successive planes; stacking faults typically form by the dissociation of \(\frac{1}{2}\{111\}\langle 110\rangle\) dislocations into \(\frac{1}{6}\{111\}\langle 112\rangle\) Shockley partials. However, the dislocation mechanism of {332}〈113〉 twinning or orthorhombic α ″ martensite is lack of a thorough understanding; there is few theoretical method considering both transitions synthetically.
The purpose of this work is twofold. First, a dislocation-based constitutive model is built for TRIP/TWIP Ti alloys to interpret the microstructural evolution led by β → α ″ martensitic transformation and {332}〈113〉 twinning. The TRIP/TWIP model was tested in a wide range of alloys, and further compared with the previous TWIP model 6 in order to explicitly clarify the TRIP contribution to stain-hardening. Second, we aim to quantitatively understand the composition-dependent phase stability and its influence on deformation modes. A pseudoelastic model incorporating thermodynamics and micromechanics was applied to calculate the threshold energy of each transformation. Extensive material information was collected and fed to the algorithm for revealing the composition sensitivity. A comprehensive computational framework is developed to link alloy composition, strengthening mechanism and mechanical response of TRIP/TWIP Ti alloys.
TRIP/TWIP alloys and deformation characteristics
Table 1 summarises the compositions, deformation mechanisms and mechanical properties of TRIP/TWIP Ti alloys. Figure 1 a comparatively visualises strain-hardening vs. uEL over three major groups of Ti alloys i.e. undergoing TRIP/TWIP, TWIP or dislocation slip. The strain-hardening accounts for the difference between the ultimate tensile stress (UTS) and the yield stress ( σ Y ). uEL is applied to describe the tensile plasticity and the value is approximated by the Considère criterion 7 . The targeting mechanical properties in the perspective of alloy design are to achieve over 300 MPa in strain-hardening meanwhile preserving more than 0.3 in uEL 8 . Most of TRIP/TWIP alloys’ uELs lie in the range between 0.3 and 0.36, whereas for TWIP alloys the number falls to 0.16 and 0.24. Stabilised β alloys or α + β alloys show negligible uEL due to the lack of strain-hardening 9 . The TRIP/TWIP Ti alloys present the best combined mechanical properties and some strain-hardening went beyond 340 MPa, while the hardening decreases to 100–300 MPa in TWIP alloys.
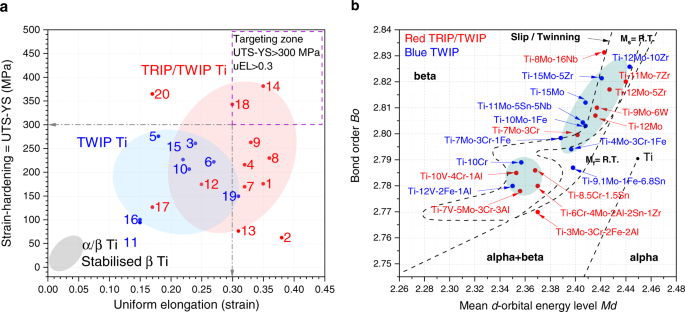
a Strain-hardening vs. uniform elongation, where TRIP/TWIP alloys exhibit the best combination of strain-hardening and tensile ductility. b TRIP/TRIP and TWIP Ti alloys are collectively located onto the Bo--Md phase stability map.
Many modern TRIP/TWIP and TWIP Ti alloys were successfully discovered with the guidance of the Bo – Md map in Fig. 1 b. The electronic parameters Bo (bond order) and Md (metal d -orbital energy level) of each element were determined by first-principle calculations (DV-X α molecular orbital method) 10 , whereas the mean electronic parameters of the alloy were simply approximated from the compositional average 11 , 12 . Nevertheless for complex multicomponent systems, this approximation is difficult to prescribe the electronic state reasonably. The dashed lines indicate empirical borders based on a small dataset 11 , which divide the map into α , α + β and β phase regions and aid in distinguishing different deformation modes. This simple mapping approach shows its efficiency in alloy design 8 . We calculated the Bo and Md values of the major TRIP/TWIP and TWIP Ti alloys, then placed them onto the plot in Fig. 1 b. These alloys with main alloying elements Mo, Cr and V group at two regions in the Bo – Md diagram as highlighted. However, future alloy development may not be limited to these regions. For example, one may develop sustainable and low-cost alloys, while preserving desired mechanical properties.
Microstructural evolution and mechanical response
A dislocation-based constitutive model was built to describe the simultaneous activation of TRIP and TWIP effects, and the detailed methodology is described in the “Methods” section. The model was validated by the alloys in Table 1 , where the tensile deformation was subjected to quasi-static strain rates at room temperature. Figure 2 shows the model validation in Ti-12Mo. The experimental data of α ″ martensite volume fraction (Fig. 2 a) were adopted from Cho et al. 13 by in situ neutron diffraction. Both α ″ martensite and twinning were activated at the onset of critical strain ( ε T = 0.013). The growing rate of f t w was significantly higher than that of f α ″ at early stage of plastic deformation. Figure 2 b represents the total dislocation density ρ raised from an initial value of 7.3 × 10 13 till 4.6 × 10 15 m −2 . The dislocation accumulation was significantly promoted by the reduced mean free path from early to intermediate deformation stage. Eventually the rise was suppressed by dynamic recovery at late stage due to the dislocation annihilation. The experimental stress-strain curve in Fig. 2 c was adopted until the onset of necking. The modelled flow stress is in reasonably good agreement with the experimental result. For comparison, a virtual flow stress curve (dash curve) subtracting TRIP effect was predicted using the same set of parameters. It displayed considerable strain-hardening although a decreased UTS was reached. Such mechanical behaviour is fairly comparable to that of Ti-15Mo 14 or Ti-10Mo-1Fe alloys 15 , where only TWIP deformation mode was operated.

a The growth of {332}〈113〉 twin and α ″ martensite volume fraction ( f t w and f α ″ , respectively) at the onset of critical strain. The error bars on twin fraction were adopted from the experimental measurement 13 . b The evolution of total dislocation density. c The experimental and modelled flow stress. The dash curve predictively illustrates the flow stress without TRIP contribution.
Figure 3 shows the model validation in Ti-10V-4Cr-1Al, a TRIP/TWIP alloy with ultra-high strain-hardening effect developed by Lilensten et al. 16 in which α ″ volume fraction was measured using in situ synchrotron X-ray diffraction. The α ″ martensite formed at the onset of critical strain and f α ″ increased rapidly to accommodate the strain. The growth of f t w was predicted by incorporatively depicting the rise of f α ″ and strain-hardening. The model well reflected the microstructural evolution and projected the experimental stress-strain curve. The strain-hardening decreased when TRIP effect was subtracted (dash curve in Fig. 3 c), indicating around 300 MPa at UTS was attributed to TRIP in Ti-10V-4Cr-1Al. This outcome corresponds to the rapid increase of f α ″ at the early deformation stage and the subsequent higher α ″ fraction.
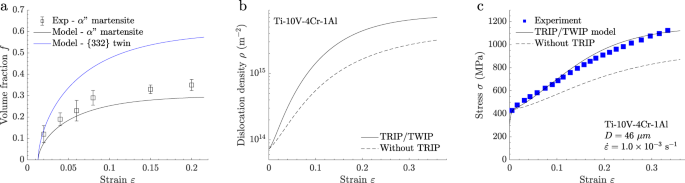
a The growth of twin and martensite volume fraction over strain. The error bars on martensite fraction were adopted from the experimental measurement 16 . b The increase of total dislocation density. c The experimental and modelled stress-strain curves, where the dash curve illustrates the flow stress subtracting TRIP effect.
The model was tested in a wider range of alloys, such as Ti-7Mo-3Cr 17 , Ti-8.5Cr-1.5Sn 18 and Ti-9Mo-6W 19 , Ti-3Mo-3Cr-2Fe-1Al 20 , Ti-8Mo-16Nb 21 , Ti-12Mo-5Zr 22 and Ti-7V-5Mo-3Cr-3Al 23 . The difference in strain-hardening was reflected on the growing rate of f t w and f α ″ (Fig. 4 ). The alloys with lower phase stability tend to display increased transition kinetics, which is facilitated by the easy nucleation of deformation products. It is known that transformation kinetics is also sensitive to external deformation conditions, e.g., strain rate and temperature, in which reduced strain rate or elevated temperature may inhibit the transformation 24 . Given by the experiments were operated within a narrow range of \(\dot{\varepsilon }\) (4.0 × 10 −4 − 1.0 × 10 −3 s −1 ) at room temperature, in this case the kinetics was solely influenced by the intrinsic phase stability. Table 2 shows the material parameters of the tested alloys. While the values of F t w and F α ″ were almost preserved constantly, the deference in strain-hardening was governed by two internal variables: twinning and martensitic transformation kinetics parameters ( β t w and β α ″ ). In the following subsection, the composition-sensitive deformation mechanisms are evaluated.
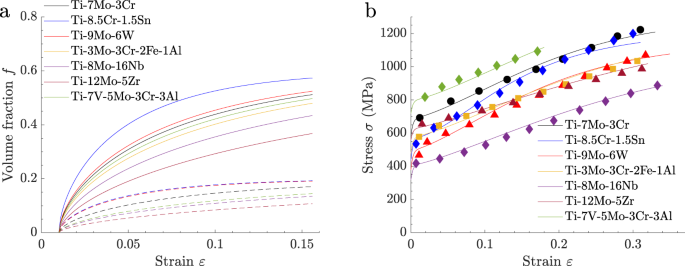
a The predicted evolution of twin volume fraction f t w (solid curves) and α ″ volume fraction f α ″ (dash curves) in Ti-7Mo-3Cr, Ti-8.5Cr-1.5Sn, Ti-9Mo-6W, Ti-3Mo-3Cr-2Fe-1Al, Ti-8Mo-16Nb, Ti-12Mo-5Zr and Ti-7V-5Mo-3Cr-3Al alloys. b The modelled flow stresses reasonably well agree to the experimental data.
Energy landscape of TRIP and TWIP
Extensive material data were collected and analysed by the pseudoelastic model to determine the energy landscape of TRIP, TWIP and dislocation slip. The current investigation not only covers laboratory-developed TRIP/TWIP and TWIP alloys, but also includes commercial or semi-commercial β -Ti alloys. The information including composition, mechanical property and operative deformation mode was constituted as a comprehensive dataset. The Gibbs free energy difference Δ G β → α at ambient temperature was calculated using TCTI2:Ti alloys thermodynamic database 25 developed by Thermo-Calc AB. Table 3 lists the input parameters, i.e., Gibbs free energy change, yield stress, elastic strain energy and frictional stress, as well as the output energy landscape. Figure 5 visualises the variation of energy landscape ΔΓ vs. the Gibbs energy difference Δ G c h e m . The alloys can be divided into three groups according to their deformation modes, and each group shows a distinctive ΔΓ energy domain. TRIP/TWIP alloys locate in the ΔΓ region of 0–1100 J mol −1 , whereas TWIP alloys distribute in a wider range of −500–830 J mol −1 . A noticeable overlapping area between TRIP/TWIP and TWIP alloys (0–830 J mol −1 ) is shown, revealing that the deformation twinning and β → α ″ martensitic transformation are mutually inclusive and the β → α ″ transformation may be activated jointly in the TWIP alloys of this area. The high ΔΓ domain (830–1100 J mol −1 ) suggesting the driving force is much higher than the opposing one, which alloys are rather metastable that β → α ″ can be easily triggered with the aid of stress. The TWIP only region (−500–0 J mol −1 ) is associated with the increased β -stability, where β → α ″ can hardly take place because the transformational resistance is too high to overcome. β -phase is fully stabilised and the alloys only undergo dislocation slip as ΔΓ ≤ 510 J mol −1 . It is worth noting that some of the alloys violate the model predictions. These alloys can be categorised into three types. First, alloy no. 20, Ti-4Mo-3Cr-1Fe, is located in the deep TRIP/TWIP region and showed typical TRIP/TWIP mechanical characteristics, such as hump-shaped strain-hardening rate over strain. Interestingly, α ″ martensite was not identified by the ex situ transmission electron microscopy (TEM) observations 26 . TEM can only observe very localised areas, besides α ″ martensite may easily revert to the β -matrix after stress release. Second, alloy No. 11, 36, 24, 25 are located close to the Slip/TWIP boundary, indicating the phase stabilities of these alloys accommodate in the vicinity of stable/metastable interface. It suggests that a transition zone may exist between the energy landscapes of Slip and TWIP. Besides, these alloys are more sensitive to deformation conditions, e.g. strain rate and temperature. Third, alloy no. 10 and 50 (Ti-8Mo-16Nb and Ti-7V-5Mo-3Cr-3Al) display TRIP/TWIP characteristics as revealed by experiments 21 , 23 , but fall into the TWIP region due to low ΔΓ. Ti-8Mo-16Nb shows significantly decreased chemical driving force compared to other TRIP/TWIP alloys due to the relatively higher Nb content. Nb plays an important role in stabilising the β phase in the TCTI2:Ti database 25 . On the other hand, Ti-7V-5Mo-3Cr-3Al exhibited a small amount of α ″ martensite as revealed by the experiments, which indicates that the β → α ″ transition was suppressed due to insufficient transformational driving force. Overall, it is possible to predict the potential deformation mode of a given composition according to the energy landscape map.
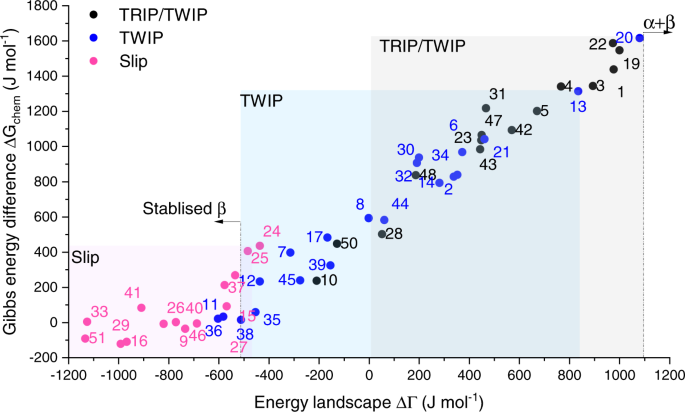
The alloys were labelled corresponding to the number in Table 3 . A clear boundary was identified between the stabilised β -alloy and the metastable alloys. The energy domains of TWIP alloys and TRIP/TWIP alloys exhibit large overlapping area, suggesting deformation twinning and strain-induced martensite are mutually inclusive for most of the compositions in this region.
The goal of this work is to build a comprehensive connection of materials information and the mechanical response of TRIP/TWIP alloys. A further important aspect is that the extensive data of Ti alloys undergoing dislocation slip, TWIP or hybrid TRIP/TWIP were analysed and fed to the pseudoelastic algorithm. Each deformation mode exhibits distinctive domain in terms of the transformational energy landscape. Within this framework, a dislocation-based constitutive model was built to interpret the origin of the exceptional strain-hardening by unveiling the evolution of α ″ martensite and {332}〈113〉 twin. The excellent combination of plasticity and strain-hardening stems from the reduced dislocation mean free path via the synchronous activation of TRIP and TWIP, as well as from the backstress generated by dislocation pile-up at obstructive interfaces.
The phase stability of Ti alloys corresponding to specific deformation mechanism necessitates a quantitative evaluation. Although the assessment of the chemical driving force may offer a rough guidance that alloys trend to be stabilised with lower Gibbs free energy difference, it can hardly provide explicit energy domains that identity different deformation modes. As suggested by Yan and Olson 27 , the current treatment unifies the orthorhombic α ″ martensite and the hcp \(\alpha ^{\prime}\) phase in terms of the thermodynamics. Given by the orthorhombic α ″ has a crystal structure intermediate between bcc and hcp, it is reasonable to describe the β → α ″ transformation as a crystallographically incomplete \(\beta \to \alpha ^{\prime}\) transformation that should have a smaller transformation enthalpy change. Although the difference between orthorhombic and hcp was not considered in the thermodynamic computation, it was reflected through the elastic strain energy. Another interesting phenomenon is that {332}〈113〉 twinning widely exists in almost all the metastable Ti alloys, which is understood by its energetically essential characteristics.
In summary, an integrated framework was developed combining physics-based modelling and data-driven informatics, which effectively links composition, mechanical response and the underlying deformation mechanism. The model takes explicitly into account the microstructural evolution by synthetically describing the martensitic transformation and deformation twinning. The flow stress incorporates the enhanced isotropic hardening by emerging obstacles and the kinematic hardening from backstress. The modelling outcome reasonably well agrees to the experimental data. Moreover, the mechanical behaviours can be captured using a set of physically motivated parameters. TRIP and TWIP modes may operate simultaneously because of the existence of a noticeably overlapped domain in threshold energy, which further indicates β → α ″ transformation and {332}〈113〉 twinning are mutually inclusive. Besides, the low shear strain of {332}〈113〉 twin makes it an energetically essential deformation mechanism for metastable Ti alloys. Our work suggests that the synchronised physical metallurgy and data-driven strategy provides an effective tool for TRIP/TWIP alloy design. Furthermore, the computational methodology shows flexible compatibility to a broad range of strain-transformable alloys, e.g., austenitic steels, Cu and high entropy alloys, meaning it may potentially serve and benefit multiple industrial sectors.
Threshold energy for transformation
β → α ″ martensitic transformation is facilitated by chemical driving force (Gibbs free energy difference between parent and product phases) and triggered by mechanical work. A martensitic embryo of a given volume tends to adopt a shape by minimising the combined interfacial and elastic strain energies. In the case of a thin martensite ellipsoidal inclusion with radius a and semi-thickness c , the overall energy barrier associated to the formation of a coherent nucleus is 5 , 28 :
Δ g s t r the volumetric elastic strain energy and Δ g c h e m the volumetric chemical driving force; γ 0 the interfacial energy per unit area of a martensitic nucleus; τ T and γ T the critical resolved shear stress and shear strain at the onset of transformation, respectively.
Martensitic transformation occurs by a homogeneous shear parallel to the habit plane together with a small dilatation normal to the plane, where complete coherency is maintained at the interface 29 . Thus the elastic strain energy Δ g s t r is divided into a shear-induced shape change \({{\Delta }}{g}_{str}^{shear}\) and a dilatational volume change \({{\Delta }}{g}_{str}^{dila}\) with: \({{\Delta }}{g}_{str}\,=\,{{\Delta }}{g}_{str}^{dila}\,+\,{{\Delta }}{g}_{str}^{shear}\) 30 . The shape change is approximated by pure shear and described as 5 , 31 :
where s the shear component, ν the Poisson’s ratio and μ the shear modulus at ambient temperature. Here, the composition-dependent shear modulus of β Ti alloys was calculated by means of the rule of mixture following Galindo-Nava et al. and Toda-Caraballo et al. 32 , 33 , i.e., for isotropic polycrystal metals μ = μ 0 + ∑ i ( μ i − μ 0 ) X i . μ 0 = 37.5 ± 1.5 GPa the shear modulus of pure Ti, X i the atomic fraction of element i , and μ i the shear modulus of element i . The latter is available from ref. 34 . The calculated shear moduli of β alloys are approximated as μ = 40 ± 3 GPa, and the predicted properties, such as flow stress and transformational threshold energy are weakly influenced by the variation of shear modulus. The Poisson’s ratio lies in a relativity narrow range for bcc Ti alloys and ν = 0.32 ± 0.01 was adopted 35 . On the other hand, the dilatational strain energy caused by volume change comes from Eshelby’s elastic field theory of an ellipsoidal inclusion embedded in an infinite elastically isotropic matrix 31 :
The dilatation \(\frac{{{\Delta }}V}{V}\) of β → α ″ transition can be calculated using a molar-volume assessment 36 :
where \({V}_{m}^{\phi }\) is the molar volume (m 3 mol −1 ) of phase ϕ ( α ″ or β ) and its value can be calculated by a linear combination of pure elements plus a regular-solution model for the excess volume 36 :
X i and X j denote the molar fraction of solute i and solvent j , respectively. \({{{\Omega }}}_{i,j}^{\phi }\) the molar volume interaction parameter between solute i and the solvent.
The martensite growth mainly results from the competition between elastic strain energy and transformational driving force. Before the applied stress τ reaches the critical revolved shear stress τ T , no transition takes place and full β phase is retained. As the load increasing and once the nucleation barrier has been overcome, the chemical volume free energy term becomes so large that the martensite plate grows radially (∂Δ G /∂ a < 0) until it hits a strong obstacle (e.g. grain boundary or twin interface). From that point, the plate starts to thicken in the direction normal to the habit plane (∂Δ G /∂ c < 0), until it achieves a state that the growth does not allow the system to further reduce its energy and a mechanical equilibrium (∂Δ G /∂ c = 0) is reached 28 . Combining Eqs. ( 1 ), ( 2 ) and ( 3 ) and differentiating energy barrier Δ G with respect to c , the equilibrium becomes:
The above pseudoelastic force balance can be simplified as \({{\Delta }}{g}_{chem}\,+\,{\tau }_{T}{\gamma }_{T}\,=\,{{\Delta }}{g}_{str}^{dila}\,+\,2{{\Delta }}{g}_{str}^{shear}\) . The current equilibrium represents an ideal energy balance in plate growth and reversal, where the transformation strain is elastically accommodated and there is no frictional resistance on the transformational interface. A frictional shear stress τ f acting to oppose the transition should be included, where the net driving force for transformation is effectively reduced by the term τ f γ T . Thence the force balance becomes:
The frictional stress is generated by the interactions between dislocation motion and solid solution; such effect was expressed by means of solid solution hardening \({\tau }_{f}\,=\,\mu {\lambda }^{4/3}{X}_{i}^{2/3}Z\) ,where λ a misfit parameter accounting for both lattice parameter misfit and the shear modulus misfit between solute and solvent, Z a temperature-dependent numerical factor whose value can be obtained from a plot of \(d\tau /d{X}_{i}^{2/3}\) vs. λ 4/3 34 . The frictional resistance term becomes positive when the plate is thickening and negative when it reverts.
In order to capture the threshold energy to trigger martensitic transformation, the energy landscape ΔΓ is defined to describe the energy margin between the transformational driving force and the resistance:
The martensitic transformation is operative when ΔΓ > 0 because the combined driving force (i.e. Gibbs energy difference and external mechanical work) is larger than the transition resistance (i.e. elastic strain energy and frictional stress) 37 . A flow chart in Fig. 6 illustrates the calculation approach. The inputs include alloy composition, macroscopic yield stress and grain size. The molar Gibbs energy difference can be obtained from a thermodynamic database. In TRIP/TWIP alloys, the radius of martensitic inclusion a initially equals to the radius of the grain size and it shrinks by the dynamically reduced intertwin space. c is the minimal detectable semi-thickness of a martensitic plate and c = 60 ± 10 nm is adopted 17 .
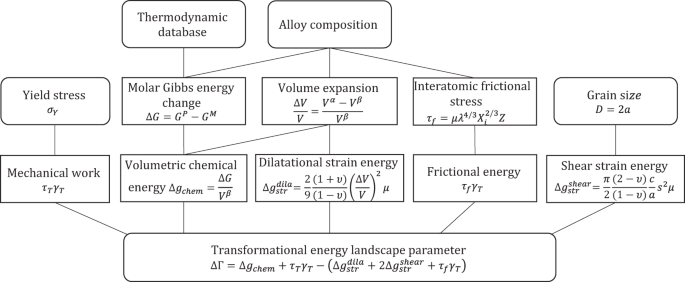
The landscape parameter ΔΓ captures the threshold energy to trigger the transition.
Constitutive model for TRIP/TWIP Ti alloys
A dislocation-based model was build integrating the simultaneous activation of TRIP and TWIP effects. In this case, the increment of macroscopic strain d ε is not only mediated by dislocation glide d ε d i s , but also accommodated by twinning and β → α ″ martensitic transformation:
where f t w and f α ″ are volume fraction of {332}〈113〉 twinning and α ″ martensite, respectively. f t w and f α ″ increase as a function of strain meanwhile consume the volume fraction of the retained β matrix (1 − f t w − f α ″ ). The shear strain of {332}〈113〉 twinning \({\gamma }_{\{332\}\langle 113\rangle }\,=\,\frac{1}{2\sqrt{2}}\) and the Taylor factor M = 2.8 representing an average texture orientation in bcc metals. Since a strain-induced ε martensitic embryo in fcc alloys with low stacking-fault energy forms by the stacking of single \(\frac{1}{6}\langle 112\rangle\) partials dissociated from \(\frac{1}{2}\{110\}\langle 111\rangle\) perfect dislocations, it can be considered that the strain accommodated by ε martensite d ε ε accounts for \(\frac{2}{3}\) of the strain implemented by dislocation glide d ε d i s being the relation \(d{\varepsilon }_{\varepsilon }\,=\,\frac{2}{3}d{\varepsilon }_{dis}\) 38 . Given by the shear strain associated with β → α ″ transition is one-half of that in a Shockley partial, it suggests that the strain accommodated by α ″ martensite accounts for a proportion \(d{\varepsilon }_{\alpha ^{\prime\prime} }\,=\,\frac{1}{3}d{\varepsilon }_{dis}\) . This gives the relation \(d\varepsilon \,=\,(1\,-\,{f}_{tw}\,-\,{f}_{\alpha ^{\prime\prime} })d{\varepsilon }_{dis}\,+\,\frac{1}{2\sqrt{2}M}d{f}_{tw}\,+\,\frac{1}{3}d{\varepsilon }_{dis}{f}_{\alpha ^{\prime\prime} }\) . Rearranging the expression it derives \(\frac{d{\varepsilon }_{dis}}{d\varepsilon }\,=\,\frac{1}{1\,-\,{f}_{tw}\,-\,\frac{2}{3}{f}_{\alpha ^{\prime\prime} }}\left(\right.1\,-\,\frac{1}{2\sqrt{2}M}\frac{d{f}_{tw}}{d\varepsilon }\left)\right.\) . Thereafter the evolution of dislocation density ρ over macroscopic strain ε can be described as:
where \(\frac{d\rho }{d{\varepsilon }_{dis}}\) represents the evolution of dislocation density in the retained β matrix resulting from the competition between dislocation storage \(\frac{d{\rho }^{+}}{d{\varepsilon }_{dis}}\) and annihilation \(\frac{d{\rho }^{-}}{d{\varepsilon }_{dis}}\) . The dislocation storage can be significantly promoted by the reduced dislocation mean free path and the interaction with dislocation forest. Thus the storage rate equals:
\(\frac{k}{b}\sqrt{\rho }\) accounts for dislocation self interactions and k is a storage coefficient; b = 2.8 Å the magnitude of the Burgers vector; Λ i the dislocation mean free path of each type of obstacle. Deformation twins or martensites can be regarded as thin circular disks according to the stereological relationship 39 :
where t i the mean width of the respective deformation product; here twin width t t w = 1.2 ± 0.3 μm and α ″ martensite width t α ″ = 0.3 ± 0.1 μm were adopted 14 , 17 . Thereafter the evolution of the dislocation density facilitated by dislocation glide becomes:
The dislocation storage coefficient k = 0.03 ± 0.005 and dynamic recovery coefficient f D R V = 3.0 ± 0.5 were obtained in this work and these values were applied to all tested alloys. The kinetics of martensitic nucleation can be interpreted by a shear-band intersection mechanism 24 , which is further derived to express the growth of α ″ volume fraction as a function of strain: \({f}_{\alpha ^{\prime\prime} }\,=\,{F}_{\alpha ^{\prime\prime} }\left\{\right.1\,-\,\exp \left[\right.-{\beta }_{\alpha ^{\prime\prime} }(\varepsilon -{\varepsilon }_{T})\left]\right.{\left\}\right.}^{m}\) . F α ″ the saturation α ″ volume fraction, m = 0.6 a fixed exponent for the TRIP/TWIP alloys and ε T is the critical strain at the onset of α ″ formation; β α ″ the nucleation kinetics parameter sensitive to alloy composition.
In addition to the enhanced isotropic hardening, a kinematic hardening term produced by dislocation pile-up should be added to the flow stress 40 . Accounting for the emerging twin interfaces, the backstress can be expressed as \({\sigma }_{b}\,=\,M\mu b\left(\right.\frac{1}{2{t}_{tw}}\frac{{f}_{tw}}{1\,-\,{f}_{tw}}\,+\,\frac{1}{D}\left)\right.n\) 6 , where n is the number of dislocation loops on a given slip plane. The flux of dislocations arriving at interfaces per slip plane in the retained β matrix is: \(\frac{dn}{d{\varepsilon }_{dis}}\,=\,M\frac{\lambda }{b}\left(\right.1\,-\,\frac{n}{{n}^{* }}\left)\right.\) , where λ = 300 nm the mean spacing between slip planes 41 . n * = 8 ± 2 the saturation number of dislocation pile-up. Analogous to the evolution of dislocation density in Eq. ( 10 ), the flux of dislocations over total strain is derived:
In both Eqs. ( 10 ) and ( 14 ), twinning kinetics d f t w / d ε is presented, which governs the growing rate of twin volume fraction. It can be obtained by differentiating \({f}_{tw}\,=\,{F}_{tw}\left\{\right.1\,-\,\exp \left[\right.\,-\,{\beta }_{tw}(\varepsilon \,-\,{\varepsilon }_{0})\left]\right.{\left\}\right.}^{m}\) over strain ε , where F t w is the saturation twin fraction.
The dislocation forest hardening led by the increase in total dislocation density is expressed by the Taylor relation \({\sigma }_{F}=\alpha M\mu b\sqrt{\rho }\) , where α ≈ 0.3 reflects the average strength of dislocation interactions. The flow stress is established by incorporating the transition enhanced isotropic hardening and kinematic hardening:
σ 0 comprises of the critical resolved shear stress of pure Ti ( τ C R S S ), solid solution hardening ( σ s s ) and grain boundary strengthening ( σ H P ): \({\sigma }_{0}\,=\,\left[\right.M{\tau }_{CRSS}\,+\,\left(\right.{\sum }_{i}{B}_{i}^{3/2}{X}_{i}{\left)\right.}^{2/3}\,+\,\frac{{k}_{Y}}{\sqrt{D}}\left]\right.G(T,\dot{\varepsilon })\) , where B i reflects the solid solution hardening coefficient and k Y = 0.87 MPa ⋅ m 0.5 is adopted as the Hall–Petch coefficient of Ti alloys 34 . \(G(T,\dot{\varepsilon })\) is a function of temperature and strain rate. The yield stress can be calculated by: \({\sigma }_{Y}\,=\,{\sigma }_{0}\,+\,\alpha M\mu b\sqrt{{\rho }_{0}}\) , where ρ 0 reflects the stored dislocation density. The validation of the physics-based modelling framework is presented in the “Results” section.
Data availability
All data generated or analysed during this study are included in this published article.
Code availability
The codes developed in this study are available from the authors upon reasonable request.
Pollock, T. M. Alloy design for aircraft engines. Nat. Mat. 15 , 809–815 (2016).
Article CAS Google Scholar
Peters, M., Kumpfert, J., Ward, C. H. & Leyens, C. Titanium alloys for aerospace applications. Adv. Eng. Mater. 5 , 419–427 (2003).
Sun, F. et al. Investigation of early stage deformation mechanisms in a metastable β titanium alloy showing combined twinning-induced plasticity and transformation-induced plasticity effects. Acta Mater. 61 , 6406–6417 (2013).
Devincre, B., Hoc, T. & Kubin, L. Dislocation mean free paths and strain hardening of crystals. Science 320 , 1745–1748 (2008).
Porter, D. A., Easterling, K. E. & Sherif, M. Phase Transformations In Metals And Alloys (Revised Reprint) (CRC press, 2009).
Zhao, G.-H., Xu, X., Dye, D. & Rivera-Díaz-del-Castillo, P. E. J. Microstructural evolution and strain-hardening in TWIP Ti alloys. Acta Mater. 183 , 155–164 (2020).
Yasnikov, I. S., Vinogradov, A. & Estrin, Y. Revisiting the considère criterion from the viewpoint of dislocation theory fundamentals. Scr. Mater. 76 , 37–40 (2014).
Castany, P., Gloriant, T., Sun, F. & Prima, F. Design of strain-transformable titanium alloys. C. R. Phys. 19 , 710–720 (2018).
Hanada, S. & Izumi, O. Correlation of tensile properties, deformation modes, and phase stability in commercial β -phase titanium alloys. Metall. Mater. Trans. A 18 , 265–271 (1987).
Article Google Scholar
Morinaga, M. Alloy design based on molecular orbital method. Mater. Trans. https://doi.org/10.2320/matertrans.M2015418 (2016).
Kuroda, D., Niinomi, M., Morinaga, M., Kato, Y. & Yashiro, T. Design and mechanical properties of new β -type titanium alloys for implant materials. Mater. Sci. Eng. A 243 , 244–249 (1998).
Zhao, G.-H. et al. New beta-type Ti-Fe-Sn-Nb alloys with superior mechanical strength. Mater. Sci. Eng. A 705 , 348–351 (2017).
Cho, K., Morioka, R., Harjo, S., Kawasaki, T. & Yasuda, H. Y. Study on formation mechanism of {332}〈113〉 deformation twinning in metastable β -type ti alloy focusing on stress-induced α ” martensite phase. Scr. Mater. 177 , 106–111 (2020).
Min, X., Chen, X., Emura, S. & Tsuchiya, K. Mechanism of twinning-induced plasticity in β -type Ti–15Mo alloy. Scr. Mater. 69 , 393–396 (2013).
Ji, X., Emura, S., Min, X. & Tsuchiya, K. Strain-rate effect on work-hardening behavior in β -type Ti-10Mo-1Fe alloy with TWIP effect. Mater. Sci. Eng. A 707 , 701–707 (2017).
Lilensten, L. et al. On the heterogeneous nature of deformation in a strain-transformable beta metastable Ti-V-Cr-Al alloy. Acta Mater. 162 , 268–276 (2019).
Gao, J. et al. Deformation mechanisms in a metastable beta titanium twinning induced plasticity alloy with high yield strength and high strain hardening rate. Acta Mater. 152 , 301–314 (2018).
Brozek, C. et al. A β -titanium alloy with extra high strain-hardening rate: design and mechanical properties. Scr. Mater. 114 , 60–64 (2016).
Sun, F. et al. A new titanium alloy with a combination of high strength, high strain hardening and improved ductility. Scr. Mater. 94 , 17–20 (2015).
Lee, S. W., Park, C. H., Hong, J.-K. & Yeom, J.-T. Development of sub-grained α + β Ti alloy with high yield strength showing twinning-and transformation-induced plasticity. J. Alloy. Compd. 813 , 152102 (2020).
Gordin, D., Sun, F., Laillé, D., Prima, F. & Gloriant, T. How a new strain transformable titanium-based biomedical alloy can be designed for balloon expendable stents. Materialia 10 , 100638 (2020).
Zhang, J. et al. Fabrication and characterization of a novel β metastable Ti-Mo-Zr alloy with large ductility and improved yield strength. Mater. Charact. 139 , 421–427 (2018).
Sadeghpour, S. et al. A new multi-element beta titanium alloy with a high yield strength exhibiting transformation and twinning induced plasticity effects. Scr. Mater. 145 , 104–108 (2018).
Olson, G. & Cohen, M. Kinetics of strain-induced martensitic nucleation. Metall. Trans. A 6 , 791 (1975).
Yang, Y., Chen, H.-L., Chen, Q. & Engström, A. Development of calphad database for both Ti-and TiAl-based alloys. in MATEC Web of Conferences , Vol. 321, 12011 (EDP Sciences, 2020).
Ren, L. et al. Simultaneously enhanced strength and ductility in a metastable β -Ti alloy by stress-induced hierarchical twin structure. Scr. Mater. 184 , 6–11 (2020).
Yan, J.-Y. & Olson, G. Computational thermodynamics and kinetics of displacive transformations in titanium-based alloys. J. Alloy. Compd. 673 , 441–454 (2016).
Green, M. L., Cohen, M. & Olson, G. The pseudoelastic force balance and its application to β -Fe-Be alloys. Mater. Sci. Eng. 50 , 109–116 (1981).
Zhao, G., Yu, H. & Petrinic, N. Deformation-induced transitions in metals and alloys. Reference Module in Materials Science and Materials Engineering (Elsevier, 2021).
Bignon, M., Bertrand, E., Tancret, F. & Rivera-Díaz-del Castillo, P. E. Modelling martensitic transformation in titanium alloys: The influence of temperature and deformation. Materialia 7 , 100382 (2019).
Eshelby, J. D. The determination of the elastic field of an ellipsoidal inclusion, and related problems. Proc. R. Soc. A: Math. Phys. Eng. Sci. 241 , 376–396 (1957).
Google Scholar
Toda-Caraballo, I., Galindo-Nava, E. I. & Rivera-Díaz-del-Castillo, P. E. J. Understanding the factors influencing yield strength on Mg alloys. Acta Mater. 75 , 287–296 (2014).
Galindo-Nava, E. On the prediction of martensite formation in metals. Scr. Mater. 138 , 6–11 (2017).
Zhao, G.-H., Liang, X., Kim, B. & Rivera-Díaz-del-Castillo, P. E. J. Modelling strengthening mechanisms in beta-type Ti alloys. Mater. Sci. Eng. A 756 , 156–160 (2019).
Mott, P. & Roland, C. Limits to poisson’s ratio in isotropic materials. Phys. Rev. B 80 , 132104 (2009).
Yan, J.-Y. & Olson, G. B. Molar volumes of bcc, hcp, and orthorhombic Ti-base solid solutions at room temperature. Calphad 52 , 152–158 (2016).
Zhao, G.-H. et al. Alloy design by tailoring phase stability in commercial Ti alloys. Mater. Sci. Eng. A 815 , 141229 (2021).
Galindo-Nava, E. I. & Rivera-Díaz-del-Castillo, P. E. J. Understanding martensite and twin formation in austenitic steels: a model describing TRIP and TWIP effects. Acta Mater. 128 , 120–134 (2017).
Remy, L. Kinetics of f.c.c. deformation twinning and its relationship to stress-strain behaviour. Acta Metall. 26 , 443–451 (1978).
Bouaziz, O., Allain, S. & Scott, C. Effect of grain and twin boundaries on the hardening mechanisms of twinning-induced plasticity steels. Scr. Mater. 58 , 484–487 (2008).
Sinclair, C., Poole, W. & Bréchet, Y. A model for the grain size dependent work hardening of copper. Scr. Mater. 55 , 739–742 (2006).
Sun, F. et al. Strengthening strategy for a ductile metastable β -titanium alloy using low-temperature aging. Mater. Res. Lett. 5 , 547–553 (2017).
Gao, J., Knowles, A. J., Guan, D. & Rainforth, W. M. ω phase strengthened 1.2 GPa metastable β titanium alloy with high ductility. Scr. Mater. 162 , 77–81 (2019).
Xu, Y., Gao, J., Huang, Y. & Rainforth, W. M. A low-cost metastable beta Ti alloy with high elastic admissible strain and enhanced ductility for orthopaedic application. J. Alloys Compd. 835 , 155391 (2020).
Wang, C., Russell, A. M. & Cao, G. A semi-empirical approach to the prediction of deformation behaviors of β -Ti alloys. Scr. Mater. 158 , 62–65 (2019).
Wang, W., Zhang, X., Mei, W. & Sun, J. Role of omega phase evolution in plastic deformation of twinning-induced plasticity β Ti–12V–2Fe–1Al alloy. Mater. Des. 186 , 108282 (2020).
Ren, L., Xiao, W., Ma, C., Zheng, R. & Zhou, L. Development of a high strength and high ductility near β -Ti alloy with twinning induced plasticity effect. Scr. Mater. 156 , 47–50 (2018).
Fu, Y. et al. Ultrahigh strain hardening in a transformation-induced plasticity and twinning-induced plasticity titanium alloy. Scr. Mater. 187 , 285–290 (2020).
Zhang, J. et al. Hierarchical {332}〈113〉 twinning in a metastable β Ti-alloy showing tolerance to strain localization. Mater. Res. Lett. 8 , 247–253 (2020).
Zhang, J. et al. Strong and ductile beta Ti–18Zr–13Mo alloy with multimodal twinning. Mater. Res. Lett. 7 , 251–257 (2019).
Min, X., Tsuzaki, K., Emura, S. & Tsuchiya, K. Enhancement of uniform elongation in high strength Ti–Mo based alloys by combination of deformation modes. Mater. Sci. Eng. A 528 , 4569–4578 (2011).
Bania, P. J. Beta titanium alloys and their role in the titanium industry. JOM 46 , 16–19 (1994).
Chen, N. et al. Reversion martensitic phase transformation induced {332}〈113〉 twinning in metastable β -Ti alloys. Mater. Lett. 272 , 127883 (2020).
Boyer, R. & Briggs, R. The use of β titanium alloys in the aerospace industry. J. Mater. Eng. Perform. 14 , 681–685 (2005).
Cotton, J. D. et al. State of the art in beta titanium alloys for airframe applications. JOM 67 , 1281–1303 (2015).
Sadeghpour, S., Abbasi, S., Morakabati, M. & Karjalainen, L. Effect of dislocation channeling and kink band formation on enhanced tensile properties of a new beta ti alloy. J. Alloy. Compd. 808 , 151741 (2019).
Zhu, W. et al. A novel high-strength β -Ti alloy with hierarchical distribution of α -phase: The superior combination of strength and ductility. Mater. Des. 168 , 107640 (2019).
Zhang, L. et al. Nucleation of stress-induced martensites in a Ti/Mo-based alloy. J. Mater. Sci. 40 , 2833–2836 (2005).
Boyer, R. R. Aerospace applications of beta titanium alloys. JOM 46 , 20–23 (1994).
Liu, H., Niinomi, M., Nakai, M., Hieda, J. & Cho, K. Changeable young’s modulus with large elongation-to-failure in β -type titanium alloys for spinal fixation applications. Scr. Mater. 82 , 29–32 (2014).
Oka, M. & Taniguchi, Y. {332} deformation twins in a Ti-15.5 pct V alloy. Metall. Trans. A. 10 , 651–653 (1979).
Wang, W., Wang, X., Mei, W. & Sun, J. Role of grain size in tensile behavior in twinning-induced plasticity β Ti-20V-2Nb-2Zr alloy. Mater. Charact. 120 , 263–267 (2016).
Wang, W., Zhang, X. & Sun, J. Phase stability and tensile behavior of metastable β Ti-V-Fe and Ti-V-Fe-Al alloys. Mater. Charact. 142 , 398–405 (2018).
Devaraj, A. et al. A low-cost hierarchical nanostructured beta-titanium alloy with high strength. Nat. Commun. 7 , 11176 (2016).
Li, C., Chen, J., Wu, X., Wang, W. & Van Der Zwaag, S. Tuning the stress induced martensitic formation in titanium alloys by alloy design. J. Mater. Sci. 47 , 4093–4100 (2012).
Download references
Acknowledgements
The authors would like to acknowledge Rolls-Royce plc for their continuing support through the Solid Mechanics University Technology Centre at the University of Oxford. X.Q.L. acknowledges the Swedish Research Council (grant agreement no. 2020-03736). N.P. acknowledges the UK Royal Academy of Engineering for Chair Sponsorship.
Open access funding provided by Royal Institute of Technology.
Author information
Authors and affiliations.
Department of Engineering Science, University of Oxford, Oxford, UK
Guohua Zhao & Nik Petrinic
Department of Materials Science and Engineering, KTH Royal Institute of Technology, Stockholm, Sweden
Xiaoqing Li
You can also search for this author in PubMed Google Scholar
Contributions
G.H.Z.: conceptualisation, investigation, methodology, modelling, validation and writing—original draft. X.Q.L.: investigation, validation and writing—review and editing. N.P.: supervision, validation, writing—review and editing and funding acquisition.
Corresponding authors
Correspondence to Guohua Zhao or Xiaoqing Li .
Ethics declarations
Competing interests.
The authors declare no competing interests.
Additional information
Publisher’s note Springer Nature remains neutral with regard to jurisdictional claims in published maps and institutional affiliations.
Rights and permissions
Open Access This article is licensed under a Creative Commons Attribution 4.0 International License, which permits use, sharing, adaptation, distribution and reproduction in any medium or format, as long as you give appropriate credit to the original author(s) and the source, provide a link to the Creative Commons license, and indicate if changes were made. The images or other third party material in this article are included in the article’s Creative Commons license, unless indicated otherwise in a credit line to the material. If material is not included in the article’s Creative Commons license and your intended use is not permitted by statutory regulation or exceeds the permitted use, you will need to obtain permission directly from the copyright holder. To view a copy of this license, visit http://creativecommons.org/licenses/by/4.0/ .
Reprints and permissions
About this article
Cite this article.
Zhao, G., Li, X. & Petrinic, N. Materials information and mechanical response of TRIP/TWIP Ti alloys. npj Comput Mater 7 , 91 (2021). https://doi.org/10.1038/s41524-021-00560-2
Download citation
Received : 01 February 2021
Accepted : 19 May 2021
Published : 14 June 2021
DOI : https://doi.org/10.1038/s41524-021-00560-2
Share this article
Anyone you share the following link with will be able to read this content:
Sorry, a shareable link is not currently available for this article.
Provided by the Springer Nature SharedIt content-sharing initiative
This article is cited by
A review on deformation mechanisms of metastable β titanium alloys.
Journal of Materials Science (2024)
A machine learning method to quantitatively predict alpha phase morphology in additively manufactured Ti-6Al-4V
- Zhuohan Cao
- Xiaopeng Li
npj Computational Materials (2023)
Quick links
- Explore articles by subject
- Guide to authors
- Editorial policies
Sign up for the Nature Briefing newsletter — what matters in science, free to your inbox daily.

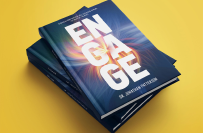
1min Video of My Solo Trip in Japan
$250-750 sgd, about the project, place your bid, benefits of bidding on freelancer.
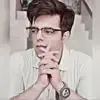
About the client

Client Verification
Similar jobs.
- Skip to global NPS navigation
- Skip to this park navigation
- Skip to the main content
- Skip to this park information section
- Skip to the footer section
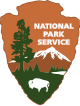
Exiting nps.gov
Alerts in effect, visiting with kids.
Last updated: August 26, 2024
Park footer
Contact info, mailing address:.
P.O. Box 40 Munising, MI 49862
906-387-3700 Munising Falls Visitor Center
Stay Connected

COMMENTS
The TRIP effect can also be utilized in forming operations, where improvements to ductility enable greater bend angles and more aggressive forming operations without cracking. The most common TRIP range of steels comprises 2 cold rolled grades in both uncoated and coated formats (TRIP 690 and TRIP 780) and one hot rolled grade (TRIP 780 ...
However, in TRIP steels the retained austenite also progressively transforms to martensite with increasing strain, thereby increasing the work hardening rate at higher strain levels. This is known as the TRIP Effect. This is illustrated in Figure 4, which compares the engineering stress-strain behavior of HSLA, DP and TRIP steels of nominally ...
The TRIP effect in these steels is pronounced at low SFE values (<20 mJ/m 2). The austenite phase forms during ART annealing and it is enriched by C and Mn to enhance its stability. By increasing the ART annealing temperature, the amount of the retained austenite at room temperature first increases, and then at higher temperatures, it decreases ...
The historic development, the principles of the TRIP effect, and the different groups of steels using the TRIP effect are described. For the already commercialized TRIP steels, characteristic chemical compositions and microstructures are discussed; the requirements for the process design as well as new annealing concepts after cold rolling are ...
The TRIP effect is the particular formation of martensite induced by forming. Here, the stress-induced formation of martensite must be distinguished from the deformation-induced formation of martensite, since the TRIP effect only sets in with the latter. This causes a simultaneous increase in hardness and formability under plastic stress in ...
In this study, two kinds of austenitic steels used in Zackay et al.'work [1] were selected to model their work.The chemical composition analyzed are listed in Table 1, which are almost identical to those studied by Zackay et al.,.In order to understand the origin of TRIP effect, we modeled Zackay's study and selected the same thermomechanical treatments described in Zackay's study [1].
The transformation-induced-plasticity (TRIP) effect in advanced high-strength steels (AHSS) can be defined as the transformation of (retained) austenite to martensite during the plastic deformation for the enhancement of both strength and ductility. This transformation substantially raises the work-hardening rate and strengthens the material ...
Transformation Induced Plasticity (TRIP) is well known as one of important effects in steel strengthening mechanism 1,2,3,4,5,6.TRIP-aided multiphase steels (TRIP steels) contain several tens of ...
Steels with TRIP (TRansformation-Induced Plasticity) effect emerged as prospective materials for car body in the 1980s as a result of intensive research of Nippon Steel.However, it took almost two decades to advance dual-phase applications (see Chap. 1), to adjust the mentality of both steel producers and carmakers, to collect more data regarding the benefits of using high-strength steels in ...
The TRIP effect is a particularly efficient strain-hardening mechanism for metallic materials, often leading to a leap forward in their mechanical properties 24. It drives the development of most ...
The Transformation-Induced-Plasticity (TRIP) effect is used for enhancing the formability of cold formable sheet steels. While the first observation of this phenomenon dates back to the 1930's ...
The TRIP effect has been thoroughly studied in ferrous systems during the last few decades, leading to success of both homogenous and dispersed austenite toughened TRIP steels [1]. Martensitic transformation also exists in titanium alloy systems, from BCC β
Zackay et al. proposed the transformation induced plasticity (TRIP) effect in the study of austenitic steels in 1967, and they emphasized that the TRIP effect is caused by an increase in strain hardening rate (SHR) due to strain-induced martensitic transformation (SIMT), but they do not specify what kind of SIMT is. To do this, we modeled their experiments of A-1 steel and A-2 steels in this ...
ENDURA and ENDURA Dual are the only wear steels with TRIP EFFECT. Because of the trip effect, chemistry, and homogeneous microstructure ENDURA and ENDURA Dual will outlast other wear steels. This means less downtime, and in some cases, a reduction in steel thickness enabling an increase in payload. To learn more about the ENDURA and ENDURA Dual ...
The TRIP effect occurs in cold mechanical conformation processes, in which the martensite phase is formed from the austenitic phase due to the stacking energetic effect [8, 9]. The TRIP effect increases the mechanical properties and modifies the magnetic characteristic of 316L from paramagnetic austenite to ferromagnetic martensite.
TRIP steels are excellent for automotive parts that require high work hardening during crash deformation and large amounts of energy absorption. They are also very well-suited for creatingcomplicated, hard-to-form parts, which is a result of their high formability and work hardening attributes. Thus, they are handy for complex reinforcement and ...
This paper presents a comparison between four TRIP steels, which belong to two groups with different chemical compositions. The first group is that of steels with a relatively low contents of Mn (1.5-2%), high Al (1-2%) and about 0.2% C, and the second includes steels with lower percentages of C (0.1%) and Al (max. 0.6%), but with high percentages of Mn (over 5%). The steels were heat ...
1) High Mn steels with varying C, Si, Al show TRIP (transformation induced plasticity) or Twinning induced plasticity (TWIP) effects. In TRIP steels, the austenite (which is stable on cooling) is ...
presence in the TRIP microstructure, it h as an important effect on the mechanical properties of TRIP steels. Si, Si, Al, P additions alone or in combination suppress car bide formation during ...
These beneficial effects, usually referred to as TRIP-toughening or TRIP-induced crack termination mechanisms, are often used along with other advantageous mechanisms to explain the exceptional fatigue or fracture properties in steels [2, 20, 21]. However, an in-depth study of the separate role of TRIP effect on fracture toughness is still missing.
Figure 3 shows the model validation in Ti-10V-4Cr-1Al, a TRIP/TWIP alloy with ultra-high strain-hardening effect developed by Lilensten et al. 16 in which α″ volume fraction was measured using ...
I am excited about the opportunity to bring your solo trip to Japan to life through a captivating one-minute video. With expertise in Video Services, After Effects, Videography, Video Production, and Video Editing, I am confident in my ability to create a visually stunning and engaging video that perfectly encapsulates your travel memories.
The mechanical behavior and TRIP effect of an AISI 304L stainless steel was systematically investigated for a wide range of austenite grain sizes ranging from 0.5 to 192 µm. The following conclusions can be drawn: (1) A transition grain size range of 34 to 90 µm was characterized, separating two distinct trends for the UTS, total elongation ...
Alerts In Effect Dismiss more information on current conditions... Dismiss View all alerts. Contact Us. Visiting with Kids. Family visiting Munising Falls . NPS photo. Pictured Rocks is a great family park. The sandstone cliffs, long beaches, numerous waterfalls, forested trails, and perched sand dunes will delight kids as well as the adults in ...
Apparently, the TRIP effect on its own mechanical properties that are inferior to those obtained when the TRIP/TWIP effect (combination of two deformation mechanisms) is used for obtaining medium-Mn steels. The combination of multiple strengthening strategies is expected to overcome the strength-ductility trade-off. In addition to TRIP and TWIP ...